Episodes
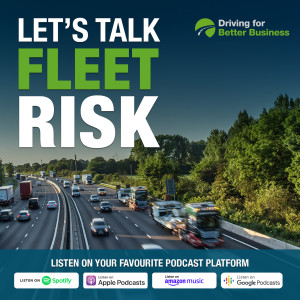
Tuesday Jun 14, 2022
Managing the transition to fleet electrification
Tuesday Jun 14, 2022
Tuesday Jun 14, 2022
Show notes: Managing the transition to fleet electrification
For Q2 of 2022, Driving for Better Business is focusing on sustainability so it seems a great idea to invite Paul Kirby onto a special edition of the Let’s Talk Fleet Risk podcast. Paul is one of the best-known experts on electric LCVs with over 30 years in the automotive sector. He’s one of the founders of the EV Café and can be seen advocating for electric vans at many of the commercial vehicle shows and conferences. Paul is also the founder of consultancy and training firm EV Essentials.
Useful links
EV Café
https://www.evcafe.org/
EV Essentials
https://www.ev-essentials.com/
Paul Kirby
https://www.linkedin.com/in/thepaulkirby/
DfBB Article: Electric vans and your ‘driving for work’ policy (10/10/2019)
https://www.drivingforbetterbusiness.com/articles/electric-vans-and-your-driving-for-work-policy/
Transcript
Simon: Welcome to Let's Talk Fleet Risk, a podcast for those who manage drivers and their vehicles and want to reduce road risk in their organisation. This quarter 2, Driving for Better Business is focusing on sustainability, so it seems a great idea to invite Paul Kirby onto a special edition of the Let’s Talk Fleet Risk podcast.
Paul is one of the best-known experts on electric LCVs with over 30 years in the automotive sector. He’s one of the founders of the EV Café and can be seen advocating for electric vans at many of the commercial vehicle shows and conferences. Paul is also the founder of consultancy and training firm EV Essentials.
Welcome to the podcast Paul.
Paul: Thank you very much Simon
Simon: Paul you’ve got something in common with our other podcast guest this month, National Grid Fleet Manager Lorna McAtear – you were both crowned Green Fleet Champions at last year’s Green Fleet Awards. What’s fired up your passion for electric vehicles, and especially electric vans.
Paul: I first drove a Mercedes Benz sprinter electric vehicle in 2004 and when you think about how long its taken for that vehicle to get here it’s incredible, but really, having driven electric vehicles over the last 20 years, what I’ve noticed is that they are such a better environment to be in and when I was working at LeasePlan the company became a member of the EV100 which is a group of businesses all committed to Net Zero by 2023 and the that sort of passion grew to help people. When I saw the environmental benefits, I also saw the driver benefit because I am a great believer in positive mental health and helping people to have a good experience in their vehicles. When you think about the driver behind the wheel of a van they often have a bad reputation but the main reason I believe for that is the stress and pressure they are under in terms of deliveries etc. Electric vehicles take a lot of that away – it’s a much better experience for the driver and ultimately, I believe electric vehicles are safer to drive than their diesel or petrol counterparts. So, there’s a number of reasons, but’s it is focused on getting the job done in a safer more efficient fashion that’s good for the driver.
Simon: You talked about the fact that electric vehicles are safer – why do you think that?
Paul: Having driven vans of all shapes and sizes over the years, if you’re sitting behind the wheel of a diesel vehicle with a gear stick and you’re trying to pull out into a busy roundabout, let’s be honest, vehicles are operating in busy city centres or towns, pulling out from junctions with various loads on, and what the electric vehicle gives you is a point and shoot. You don’t have to worry about changing gears or being in the right gear - you can put both hands on the steering wheel and go, whereas in the diesel vehicle you’re having to do a number of things. You could be in the wrong gear for the weight in the back etc. That was the first thing and also, we drive more carefully in an electric vehicle because we’re conscious of preserving range, I think we’re more relaxed. A study was done on London taxi drivers that said they were happier, which is interesting, they were calmer and more focused on the wheel of an electric LEDC range extended electric vehicles. They were delivering a much better experience and so those are the main reasons I believe it’s safer to driver an electric vehicle.
Simon: The driver wellbeing is interesting – we’ve done a lot of work with CALM – van drivers are predominantly male, and CALM is aimed at preventing male suicide. It can be a very lonely existence - so making that environment nicer – and the electric vehicles are certainly pleasant places to be – so it’s probably an underestimated benefit.
Paul: I agree with you completely, CALM – the campaign against living miserably – I love that acronym. It’s such a ‘does what it says on the tin’ kind of description. I love that and the charity’s focus. When you think about the suicide rate of men it’s the biggest killer of men under 40 I think and men are our predominant driver population so the fact there are wellbeing benefits – it points to getting the drivers engaged early on in any approach we take to electric vehicles because they will understand the benefits.
Simon: The other point in terms of being safer to drive, when I spoke to Lorna who runs one of the biggest fleets in the UK, I’d expect her transition to electric vehicles to have seen possibly an increase in collisions as people go used to a new experience. Her experience was that people were more cautious and drove more safely and making sure that the charge lasted as long as possible they drove more safely, and her collision rate went down. Is that your experience?
Paul: Yes, what we know is that the vehicles are typically easier to drive, and drivers are calmer – that whole ecosystem works well. Insurers are even saying that you’re 25% less likely to be involved in an accident in an electric vehicle and this experience mirrors everything that Lorna has said. I wouldn’t disagree with any of it – it’s absolutely the case. Anybody I’ve come across driving electric vans are finding it a positive experience. But I will say getting the driver engaged in the first place will make or break that transition. We also hear stories when vehicles are demonstrated and drivers take them out into the big wide world, they are nervous – they say it doesn’t work – 1. Because it’s different, 2. Because they have to do things differently and charging becomes an issue because if you have only ever driven a petrol or diesel vehicle and you’ve only ever turned up at a petrol station to get your fuel, you may have never noticed the funny looking boxes with cables, that will power your vehicles, so you go into it with trepidation, so I think getting them onside in the first place is critical to a successful transition which will ultimately benefit the vehicle and the driver.
Simon: I know that some really big fleets are on their journey to complete electrification of their fleets by anywhere between 2025 and 2030 but it seems, there’s a lot of small businesses who don’t really know how to start. They maybe have a small fleet of diesel vans – what should they be thinking about – what are the challenges they need to think about now in order to transition as a smaller fleet to electric vans?
Paul: I think smaller fleets are slightly more challenged than the larger fleets as they tend to have predictable journeys and routes and mileage. They also have professional teams of fleet managers and probably experienced board members, finance execs, facilities people – all of those stakeholders who are needed for this transition. So, I think smaller businesses, if I take my own experience of stepping into business myself, there are a lot of questions you don’t know the answer to. There’s a lot of help out there – online and potentially people can come and talk you through the process, but you need to engage with a wider stakeholder base, starting by talking to landlords – you might say why? – but you talk to them because you need to think about charging. It’s the first thing to consider. You need to put in your own charging points, you’re not going to be reliant on the fuel station down the road. You will be putting in charging infrastructure in your own car park, premises – because we would want to be in maximum control of our own destiny when it comes to charging. Charging in the public domain at the moment is still somewhat of a concern because you can’t always guarantee you get on the charge points, and you can’t always guarantee they’re working. It’ s okay for most of the time, and it’s okay for a car – but when you’re in a van there are other challenges, so getting control of the charging experience is one of the first things you should do, almost before you think about vehicles. Can I charge whatever I buy? That’s the first question. Then you can start thinking about the vehicles and when you do, then it’s considering the data behind what you’re doing. I’m not a great fan of data, I’m a great fan of insight that data is essential for, but because I’m not a the most detailed of people I enjoy the opportunity to take data and then to turn out an answer than says these were the routes you have done, this is how many miles, this is where you’ve been and by the way if you put a charger here it would enable you to get additional charge in the place where the vehicles spend the most time. But whatever you do, it’s key to just get started, get demonstration vehicles, to engage your drivers, to find champions in your business who may be very positive about electric vehicles and will help you in your own transition because they’ve got a electric vehicle at home.
What we’ve seen from the big fleets there is a lot more people now that are van drivers, sparkies, electricians, chippies, that are working within big organisations like British Gas that can then share their experiences as well, so we’re seeing this cascade of experience coming into the van world, and more and more people are waking up to it.
Simon: It’s especially helpful to get as much information from as many people who have used electric vehicles as you can – help you understand to meet the challenges.
Are electric vans right for everything?
Paul: It’s a definite ‘no’ – whilst we have a lot for solutions for van users, many use cases are already very much sorted, but there are those when there is a real challenge. Towing in civils or construction is one case. If you’re using your van to move your diggers, that’s not going to be an ideal scenario because there is no electric vehicles that can tow considerable weight currently. By considerable I mean over 1500kgs. That means quite a lot of small business where they are multi using the vehicles – many times the vehicle goes out without towing, but it won’t do those critical jobs which means that you can’t really justify going to electric vehicle unless you take the blank canvas approach and get back to basics. How do I do my business? Is there another way that I can get that digger to the site or is there another way that I can do a particular job. Long trunking, if you’re doing 350 -400 miles in a day it wouldn’t be my recommendation to be thinking electric just yet, unless you have considerable amounts of time.
That said, with the public charging improving you can take time out of your day to have a break and you should be taking time out to do that, as I’m sure DfBB advocates, a decent break during the day – 45 mins – you could use that as your ideal charging time, and you would get certainly another 100 miles, because there are decent range vehicles on the market, but it’s not enough for some.
Simon: One of the things that Driving for better business espouses is better management of those that drive for work because of the benefits - understanding and managing those risks better - in a traditional vehicle those risks are predominantly the driver’s ability to check the vehicle and make sure its road worthy before they go out and then to competently use it in a safe manner, so with electric vehicles what are the differences as far as vehicle checks go and what driver training is needed to effectively use an electric vehicle?
Paul: In an electric vehicle it’s simply an ICE vehicle with the engine taken out and the fuel tank taken out and a motor put in and a battery put in – that’s basically the difference. Obviously there a few electrical bits and pieces that connect it all up and a charge point rather than a filler cap – so there are a lot of things around the van that are exactly the same. It’s very important to be still checking your tyres – arguably more so because your tyres are on vehicles that are typically higher powered than their ICE counterparts. Diesel vehicles don’t have the same amount of power delivery from the moment you put your foot in the accelerator. So tyres are an area for focus because there is a potential for higher tyre wear.
You would l check everything else – washer fluid, lights, glass, mirrors, make sure that you do all of the normal daily checks. You just don’t have to do the oil anymore which is a good thing, right? Your version of the oil check is to check you have enough range to do the day’s work. Making sure the vehicle is charged and you have your charging cable because if you go out and about there are some chargers – the rapid chargers – have fixed cables but if you turn up at a customer and you can charge there, you might need your cable. Making sure your charge port is not damaged – just making sure your vehicle can function while you’re out if you need to charge – those are the key things. Obviously, driver training – this is a fabulous opportunity to really engage the driver. They are approaching something they haven’t done before – a new way of doing things so this might be a time where your driver is more receptive to driver training and getting the best out of the vehicle. They know it all with a diesel vehicle but you put them in an environment where they are not quite so sure you can school them from the beginning and give them an opportunity to absorb better safer driving that is synonymous with electric driving.
Simon: Many fleets are used to telematics data from their fleet to determine driver training requirements. Does telematics still work in EVs, and do EVs have their own new data streams available? Do telematics systems still work with electric vehicles or do they have their own data?
Paul: The electric vehicles themselves are a little different than their internal combustion engine counterparts. They’re working on different protocols so whereas you could just plug in to the OBD and a lot of data would be taken from the vehicle, it’s not quite as easy anymore. For some reason the manufacturers have taken an opportunity because they don’t have to have an OBD they’ve taken the opportunity to do their own thing and go off piste if you like.
More reverse engineering has to happen and there is some incredible data you can take from electric vehicles around the battery – how it charges, whether it is charging and all of the usual driver behaviour type of things like hard acceleration, harsh braking, how they corner, all of that information is still there. What we do know is that manufacturers are keen to create their own data streams so they are looking at ways of putting it into the vehicle – certainly Ford are doing that currently. Mercedes have done it for some years now and it will be more important in electric vehicles as well. They are trying to take the data and sell it in a way to the wider market so broadly speaking, data is available, certainly for the driver behaviour piece, but it is different and there are things that are changing and I think the typical telematics providers will become data management companies. Taking the data from whatever source and then doing the science ion the data so they can produce the insight we need.
Simon: One of the things that is topical is the cost of fuel and energy, with fuel at record prices and cost of energy is going up from events around the world - how does that affect any financial decisions for a switch at the moment
Paul: You mentioned the EV Café earlier and we did a session when the price cap went up for domestic energy and all the noise, and the horrific world situation, and it’s a two pronged tragedy in that all prices are going up so everyone is affected at all levels at society so whether you’re in business or a private individual, you’re being affected by the increases in the cost of living. Fuel going up and electric going up means that the gap is still there and still significant. The gap when you’re paying for public charging verses fuel is narrowing but generally speaking, the cost per mile of fuel – electric vehicle vs diesel is definitely considerably less and makes that total cost of ownership argument still stack up broadly speaking.
I think the total cost of ownership is something people have to get their heads around. You’ll pay more in the short-term for the vehicle – that will change over the next 2 to 3 years potentially, but in the meantime what you’ll see is that the cost of energy will mitigate the overall cost of running that vehicle. Also, as we talked about the reduction in accidents, the driver wellbeing, I think people will be less off work – there’s a lot of soft benefits. The other key benefit when we think about total cost model – energy is going up as is fuel, the cost might be narrowing but the other benefit is down time. The scourge of every fleet manager – down time really impacts a business and can cost a business significantly. I was talking recently at an event and asked the question, what is the cost of downtime? Many times, even fleet managers don’t know, but one lady in the room said it costs me £300 per day for planned downtime and £1500 a day for unplanned downtime – so downtime has a significant cost. Averages can be £750 - £800 a day with much research behind that which is possibly surprising so when you can reduce downtime because the maintenance levels are much lower – the fact they don’t have an engine with just a few moving parts rather than thousands. This makes a massive difference in time and costs, so when you’ve got the whole cost of ownership not just focusing on fuel, it makes a really big difference to your cost model when you’re looking at an electric vehicle.
Simon: That’s an excellent way to finish our discussion – one of the key benefits off road time and down time is the biggest thing when I speak to fleet managers. A final question, What would be your first steps for any fleet managers or business owners looking to start their switch to electric vans
Paul: I would say that you could get a really good consultant, my website address is... just kidding. I would look around for help in your peer group first of all. The community of fleet managers and community around electric vehicles is a really friendly place. Once you’ve reached out and asked those questions, look at vehicles and get data on your journeys so you understand longest and shortest journeys so you have clear understanding of what your fleet does today, what it needs to do tomorrow and engage your drivers early on because they will be really good advocates. Then try some vehicles. Where possible try vehicles where you can also get a good experience on the charging, charging is key – making charging a part of the plan is essential and engage with the wider business to make sure you have all the stakeholders round the table and onboard. There’s a lot of insight and information out there on this transition and if you’re unsure – reach out to somebody that can give you advice, or maybe support you long term in that transition.
Simon – Excellent advice and I will put links ion the show notes to both the EV café and the EV Essentials website, and I guess anyone who would like more advice from you can get in touch with you via LinkedIn
Fascinating – thanks very much Paul
Simon: If you manage drivers and their vehicles and you face similar issues to those discussed in this podcast, there are links in the show notes to some useful resources on the Driving for Better Business website, and these are all free to access. If you enjoyed the conversation, please don't forget to hit subscribe so you know when the next episode is released, and please also give us a five star review as this helps us to get up the podcast rankings and makes it more visible to others who might also find it useful. You can follow us, that’s Driving for Better Business on Twitter, Facebook, and LinkedIn, and most importantly please help us to spread the word. All our resources are free for those who manage fleets, and their employees who drive for work. Thank you for listening to Let's Talk Fleet Risk, and I look forward to welcoming you to the next episode.
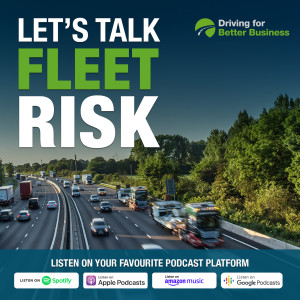
Friday May 06, 2022
National Grid - Net Zero by 2030 - Spotlight on Sustainability
Friday May 06, 2022
Friday May 06, 2022
Show notes: National Grid - Net Zero by 2030 - Spotlight on Sustainability
Transcript
Simon: Welcome to Let’s Talk Fleet Risk – a podcast for those who manage drivers
and their vehicles and want to reduce road risk in their organisation.
My guest today is Lorna McAtear. Lorna is the fleet manager for National Grid – Hello Lorna and welcome to the podcast
Lorna: Thanks Simon. It’s great to be here.
Simon: Since we started this podcast last year Lorna you were one of the people I really wanted to talk to, but before I say why, could you start by just giving us a quick overview of the size of the National Grid fleet and the types of driving your staff are engaged in.
Lorna: I joined National Gird 2.5 years ago – we had 3000 vehicles on the fleet, 1700 company cars – only 7 were electric vehicles, so we’ve been on a massive transition through that. We have over 1000 commercials of which 350 are 4 x 4 and more recently, part way through last year we merged with WPD, so in total now we have 9000 vehicles, of which there are an awful lot more 4x4s and a few helicopters, so the transition is a large fleet now to manage.
Simon: We’re publishing this podcast in May 2022 and one of the reasons I wanted to have you on as a guest is that we’re putting the spotlight on sustainability. Driving for Better Business campaign is promoting a series of resources as well as case studies of fleets that have reduced fuel use and emissions – through either reduced mileage, more efficient driving or electrification of the fleet. You’re one of the best known advocates for electric vehicles and reducing emissions. National Grid as a company is aiming for Net Zero by 2050 – how does your fleet strategy fit into that?
Lorna: That was one of the first things I did – to design that fleet strategy and interestingly I was pushing the fleet strategy for a 2030 target when the legislations was for 2035 so there were a few challenges around why I was picking that date, but I think when you’re close to the marketplace you can see where the changes are coming in. I put together the plan for the next 10 years – knowing what I can control within in it. The 4x4s I mentioned, I know I can’t do anything about that. I can retrofit but there isn’t anything really, I can do for the vast majority on fleet, so it’s planning for a date in 2024 or 2025 knowing when the changes are going to happen. So, what I had to do is work with the enablers – what were the education programmes I needed to put in, that whole communication piece around it, which vehicles could I tackle immediately, which vehicles did I look at later – and just map put for everybody so we knew exactly when and where things were going to change. All I’m doing now as the years go by is sense checking into that original plan and working out whether I’m behind or ahead and is there anything else I can now do because of innovations that have come to market. Can I change some of my commercial vehicles earlier than I planned? There’s a whole raft of things that went into that but the key was having the plan in the first place and getting buy in.
Simon: Are you trying to replace the fleet vehicle sin line with your natural vehicle replacement cycle?
Lorna – Absolutely. You don’t need to get rid of the vehicles straight away. Just follow that replacement cycle so the whole plan was geared around that we mapped out every single replacement ad some of them have got checkpoints on so the heavier the vehicle is or the more ancillary equipment it has, it just a checkpoint in time and it may be t at actually we extend that vehicle because the different vehicle will come out later, so each time I have a replacement it triggers a conscious decision on are we replacing, or are we intending to do something different?
Simon – presumably helicopters present a challenge in their own right
Lorna – haven’t got a clue on that yet!
Simon: From a driver competence point of view, I had a week in one as part of a campaign we were running and there are some obvious differences, such as what you would check, and the driving characteristics – there are some obvious differences involved in driving an EV from the pre-use check angle as well as driving characteristics.
How does National Grid communicate these to drivers and how you liaise with colleagues responsible for driver safety on the training requirements for EVs?
Lorna: Stories are great aren’t they. The one thing is obvious is they are automatics. The first time I drove an electric personally was a Peugeot van and I nearly stuck my bosses head through the windscreen because I never driven a automatic before, so you learn from experience, and you can use those stories to relate to people. Its’s how you get that communication out there, and it’s how you normalize things. There are a lot of things we do with our ICE vehicles that don’t change even if you you’re in an EV. You’re still doing your normal drivers checks, tyres, make sure your windscreen wash levels are topped up, the FLOUR acronym, and we had some real challenges. Most of our EVs went onto the fleet during full lockdown during COVID so we had to do a lot of the driver education through peer to peer talks, through actually standing outside the vehicle and explaining things. There was a lot of online things because you’re right, understanding that regen you really can’t explain it to someone until they felt it themselves and they feel that vehicle so it’s just trying to work out pretty much with the whole sustainability plan what can you do, when can y you do it, which drivers adapt easily, some of the drivers already had EV cars so an EV van wasn’t a problem. So how do you identify your higher risk drivers and then make sure that each of the education pieces are there. What we did was a lot of hand holding to start with because it was new to us. It was new for us to educate others. We weren’t sure what education we needed. You’ve always got challenge – they can get uppity if you want to give them some education so it’s how you go about that.
Simon: How do you deal with an incident like a breakdown, or a collision – when things are different with an EV. Unless you’ve been told you might expect to be able to do certain things…
Lorna: Again. Some of that is already in our policy anyway, some of the base policies – fleet managers should check all the base policies and reinforce those because you’ll find an awful lot of it already covers those nuances between the EVs and you’re using breakdown providers, they know what they can and can’t do. So one of the things I did on that, when I was at Royal Mail and we’re doing it here – when we’re doing mass rollouts we notify the breakdown provider in that location so they can gear up to make sure that provision Is there. But what I am finding is that they don’t breakdown!
Simon: Well, that’s handy
Lorna: They’re far better – you have far less mechanical issues. Less moving parts, people drive them better, more cautious to start with as well, it’s quieter so the indirect benefits are people’s wellbeing. Drivers are less stressed out, the old fashioned ‘white van man’ goes, people are interested in how you’re looking after the environment, so the public perception is better for the drivers as well, all those things make for a better wellbeing type of environment, and it all comes into how they driver the vehicle.
Simon: I was wondering if you’d seen any changes in collision levels with the EVs? Are drivers more prone to collisions, maybe as they get used to the vehicles, or have you not seen a difference? Sounds like you’re not seeing that.
Lorna: We’re not seeing that at all. It helps that you can’t get a replacement EV so don’t damage it in the first place! We are seeing drivers look after those vehicles better so we are seeing less incidents. Don’ forget they come with a lot more safety features as well
Simon: They have pretty much a full suite of collision avoidance tech as a whole?
Lorna; Vans always used to be the poor relations to the cars, there’s a lot of that tech coming in now – blind spot indicators, a lot more coming in to the vans with the EV tech.
Simon: One of the primary challenges with electric vans has been reduced load carrying capacity due to the weight of the battery, which can lead to over loading. Has that been a problem for NG?
Lorna: No, because we before we put them in, we did that assessment of the specification and used it as an opportunity to reassess how you do the job. You’re not taking what you did before and just replicating it. You’re taking it as an opportunity to say what can I do differently. Can some of that kit come out because when you look at it you realise the kits has ended up in the vehicle over they years and it’s become habit. When you go into it you don’t need it – you find you’ve been hoarding stuff. So you just change the way of working and have a look at the vehicle and go back to basics. Because we knew we could not get EVs in the larger sizes when we first started, we looked at the vehicles and said – what do you actually need? If we put the ladders the site instead, can you reduce the weight? There was a lot of work in designing specifications first to make sure that everything came in as it should.
Simon: It’s a great lesson for any fleet – it illustrates the need for constant vigilance and management of what you’re doing, not letting bad habits getting ingrained, or adverse trends become the norm. You want to keep monitoring everything you do, and go back to basics to keep it fresh and ensures everybody is on top of their game
Lorna: We’ve done that with the recent highway code changes as well, so the legislation changes on the mobile phones, the access ways with pedestrians we did a huge internal campaign. Every change gives you an opportunity to go back and re-educate or reinforce some of your key messages. I know with the mobile phones changes, all we’re doing is reinforcing something we already had. Take very single change as an opportunity to just double check you’re up to speed . For example we did it recently, we had the mini fuel crisis, driver shortages, we dusted ff the business resilience plans and there was no provision in there for EVs and we had ramped up that fast, when the fuel was running short, we didn’t need to worry as much as we did before, because we had a lot of electric vehicles to use as shuttle vehicles or to do sme of the other jobs, we had different locations – so go and use their vans – so we ended up changing our business resilience plan to also factoring that we had EVs.
Simon: I watched the Transport session at COP26 in Glasgow last year where you were a panel member and you said you thought range anxiety had gone away, because the average range of an EV is now well over 200 miles, and the main concern now is charging anxiety. From a driver management perspective, any kind of anxiety can lead to a lack of concentration or distraction behind the wheel so does National Grid look at any of this from a driver wellbeing/confidence angle? How do you manage that? Have you go enough infrastructure.
Lorna: I think we have gone from range anxiety to charge anxiety and we’re now into a space where there almost an etiquette that needs to come in. There are so many more vehicles charging – you’re expected to move at 80% charge, but vans have less charge available to them and 90% is what’s needed for them to finish their job for the day and there’s an understanding creeping in. Car drivers – we are putting the infrastructure in and sorting out the depot charging for the commercial vehicles. We’re providing some charge point cards and we notify the drivers where there public charge points are, so we are trying to help them in the same way that we would with an ICE vehicle. A lot of stuff managing risk, anxiety, driver wellbeing are already there – they might need the odd tweak so it’s reinforcing it again.
Simon: You’ve still got a considerable number of ICE vehicles on fleet, petrol, diesel, as you work towards net zero, so you do you do anything around helping drivers use those vehicles more efficiently.
Lorna: Yes, we always do things like that – reducing high risk levels, increasing compliance, reducing accident rates – you’re always education people on driving better so you’re always reminding them that heavy right foot – trying to get from A to B as fast as you can, especially when you get emergency callouts – it’s reminding people that you drive like that, it’s different between electric cars and vans and once they’ve learnt that, some of that actually creeps back into their vehicles when they’re driving the ICE vehicles. We are seeing natural transitions, but we still go out and remind people. We have safety briefings, we’ve trained over 10,000 drivers in road safety in 5 years, we’ve checked over 50,000 licence checks and we’re increasing that again so it’s a continuous piece of work that you cannot afford to stop doing because you ever quite know what’s next. We have got all of these fuel concerns going on so it’s going back and reminding people how to conserve your fuel. Every one mile an hour over affects your MPG.
Simon: DfBB is primarily about communicating the business benefits of good management practice, vehicles or drivers, so could you quantify some of the reductions you’ve achieved in fuel use and emissions as you near your net zero target?
Lorna: Some of the initial targets were just how many EVs – of the 1700 cars 700 are fully EV. October last year, was the first time the number of pure EVs was higher than the number of ICE cars so we had tipped the balance. We have a bunch of hybrids in the middle. I’ve got less than 400 ICE vehicles on the car fleet. In terms of the commercials, what we’ve seen in changes there, it comes back to the point, when you’re educating the drivers on fuel consumption and everything else you are seeing the numbers go down, how we measure some of it – our average co2 per km is 55g now, which is one of the lowest going, especially if you haven’t got pure EVs. We are seeing fuel, economy, emissions but I’m also seeing reduction in my incidents, the number of things happening and where the fault is changing in the right direction. That awareness level means people are much more conscious now of how they drive. They are in the public eye more. If they burn that fuel they are damaging that air quality and that’s become something that people value.
Simon: More fuel-efficient driving tends to lead to safer driving – has this led to any reductions in collisions, or any other business efficiencies such as lower maintenance costs? You mentioned earlier less was going wrong. Less to spend on damage repairs? You’re seeing some string financial benefits and efficiency benefits?
Lorna: Yes – of course you use that at the beginning when you’re doing you’re total cost of ownership. We’ve all heard it – the upfront cost of these vehicles is more but if you use everything you said and factor that in your total cost of ownership very often is lower. The other thing we notice is that you can keep these vehicles longer if you chose to do so because there’s less to go wrong. The tech is there. You factor that into the total cost. Right now, personally, I would say it’s still a no brainer to go Electric Vehicles.
Simon: Excellent. Final question – What would be your advice to fleet managers, on where to start with the risk management, to other businesses who might be starting out on their net zero journey?
Lorna: I’m often asked this – and you talked about the risk management. You need to make sure you educate your drivers and you need to remember there’s an awful lot you’ve already got I place so just go through your own policies and make tweaks to it. Don’t try and reinvent the wheel. For anyone who’s starting out, there are so many resources out there – National Highways have loads of resources – toolkits for drivers and risk so just take those resources and use them and adapt for your policies.
Simon: Lorna – I’ve really enjoyed that discussion thank you so much for being on the podcast
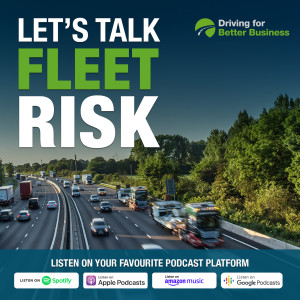
Thursday Apr 14, 2022
Overcoming the hurdles to good driver safety management
Thursday Apr 14, 2022
Thursday Apr 14, 2022
Show notes: Overcoming the hurdles to good driver safety management
John Andersen is the National Logistics Director for Tarmac, and manages one of the largest supply chains and fleets in the UK, working across the rail, road and water sectors.Tarmac operates a mix of vehicle types. In this podcast John talks about communicating the risks to his drivers effectively, and overcoming the hurdles to good driver safety management.
Useful links
Tarmac Case Study
https://www.drivingforbetterbusiness.com/case-studies/business-champion/tarmac/
Transcript
Simon: Welcome to Let’s Talk Fleet Risk – a podcast for those who manage drivers
and their vehicles and want to reduce road risk in their organisation.
With me today is John Anderson. John is the National Logistics Director for Tarmac and manages one of the largest supply chains and fleets in the UK working across the rail, road and water sectors.
John, Tarmac operates a mix of vehicle types. To start with could you give us a breakdown on the size of fleet you operate, and the type of driving the business needs to manage
John: As market leaders in the construction industry, we manage materials supply. As a major supplier to the UK infrastructure, we manage a fleet of around 5000, half of those are large goods delivery vehicles but also 2500 are light commercial vehicles or cars and vans which our employees use to travel to and from their place of work.
Simon: That’s a complex fleet to manage. What have been your main challenges in identifying areas for improving driver safety and how have you met those?
John: We risk categorise each of those and we focus on the large goods vehicles. We cover in excess of 50 million miles per year making hundreds of thousands of deliveries per month. As such, these vehicles work on site, on the public highway, and offsite as well, so there’s a whole range of risks associated with this, not just the physical risks but also the behavioural and psychological risks around operating these vehicles. Our initial focus is around some of the generic issues – speeding, around harsh braking, control of the vehicle and we make sure that we are satisfied that the people operating these vehicles are competent to do so
Simon: Do you get any driver input into what the actual risks are with the different types of transport movements?
John: We do, we try and engage heavily with the drivers. I think this is a very valid point. Historically our engagement and involvement with the drivers tended to be around negative events, and I think it’s a real reflection and something that’s been part of the Driving for Better Business approach. Historically our involvement with drivers was a result of a negative event – an incident, an accident a road traffic collision or a speeding event, whereas now we are really broadening that, and I think it’s something that COVID has bought to the forefront. So, ‘hang on a second, these people do million of miles in their daily lives, representing our brand and delivering our products and are very much customer facing’ so we realise we have to engage with them. We make a conscious effort to engage in a positive way and make sure that communication is 2-way – so monthly newsletters for example, we really celebrate some of the small things these people do to deliver successfully and be part of our brand, and make sure that they have the ability as part of the delivery system to report good acts as well as negative acts – so near hits or near misses, they can submit that electronically from their vehicle and we look to give them recognition on the positive events as well. Drivers are on our health & safety committees and in our site liaison meetings. We involve them in the discussions and our plans and future thoughts.
Simon: So getting drivers to report near misses must have been quite a challenge. They have to feel they’re properly supported form the top, or else there’s a risk they feel they are reporting something that will get them into trouble. You must have done well with the driver culture to get them to feel comfortable reporting near misses – that’s great as it gives you more data to work on to make them safer.
John: I think you’re right. That’s a been a fantastic success. First of all we automated it – made it easy and initially we made them anonymous but actually we find people put their names, sites, locations and are proud to say they are part of that campaign. If they see something is not working, they step in and again no one wants a negative outcome. One of our key foci is whether they’re driving, in an office, on a machine or on a customer site and they see something that has potential to cause harm, they make a conscious decision to report it and I believe they now realise it makes them feel better about themselves and better about working for our organization.
But there’s no doubt it’s been a challenge and there’s no question that culture was there, but once you get over that it’s about the safety element and people’s wellbeing, I think that starts to gain traction and we see that grow every month. Then you make data driven decisions. Those data driven decisions make sure your strategy and your policy are heading in the right direction and aligned to where the real challenges are about people who drive for a living.
Simon: What’s the secret to communicating your key risks effectively with the drivers to try and achieve that?
John: I think if we go back to the year before COVID, 2 years before COVID, we had a big campaign where we went out, we had stickers, various giveaways for our hauliers and drivers and we went out to our sites and offices and spent time actually talking and listening – again it was trying to be proactive rather than reacting to a negative event. We launched it and advertised it and, in the end, people were nominating and requesting us to go to their sites to meet and talk about some of their concerns. People were very proud about some of the things they had done, the best practice, and they wanted to show it off and we encouraged the transport teams, the distribution teams, the depot & warehouse teams to get out there and talk to the people who are representing us every day, get on the front foot and listen to them and that really has driven that collaboration forward, and got them to a position where trust in the senior leadership team, in the people they deal with every day is important. We certainly would advocate the quickest way to build trust is to get in front of your people and talk to them – and listen That’s important. My motto is ‘you said, we did’ – it’s important that if we agree to do something we do it, and they can see that, so that certainly starts a journey and is something you can build on.
Simon: That’s obviously a good example of how you communicated to the drivers – there’s basically clear standards set that the drivers understand that they need to follow, they understand why, they’re trying to follow these standards and to maintain high levels of professionalism with their driving. You touched on the fact that it’s important to recognize the good. Can you give us examples of how you recognize good behaviour in practice, and how do you provide feedback when someone has fallen short?
John: We employ our own drivers, and we also have third party contractors so we engage with the key people in that organization as well as the individuals driving the vehicle. We do get regular reports from LinkedIn or Twitter, through communication, through social media channels and we make sure someone in a relatively senior position will pick up the good feedback and speak to the haulier and make sure they speak to the driver, Quite often, myself I will often drop that driver an email or a phone call to say we’ve had a report that you slowed down for some horses and we got really good feedback from those riders, ‘the Tarmac Trucker was the most considerate driver they’d passed’ – and that’s great feedback and we send that to the driver and the employer but also to the local site, and I think again trying to promote that local ownership and recognition that driver s representing them and the brand and who we are as a logistics function.
So some good opportunities to celebrate success there. There are small tangible things they get a body warmer or a fleece or a cap – just some small things.
On the negative side, we recognize people make mistakes or misjudgments, it is making sure we don’t overly penalize that but that people are aware they have gone wrong, why it’s important that they rectify that and we put measures in place that we’ve had that discussion, we’ve implemented that action. But it’s following up on it. We know that some of the biggest risks are when things are not followed up and it creeps up and becomes a repetitive event and that’s something we revisit with the help of some of our technology – and hopefully we prevent a recurrence.
Simon: With Tarmac being such a large organization and, with a supply chain working under the Tarmac banner that also contributes to a significant number of transport movements, I’m wondering how you ensure the various layers of management within Tarmac, and your suppliers, understand and meet the standards that you’ve set?
John: Again, it is complex, there’s no question. We supply hundreds of different products in various vehicle types, and we manage that on a matrix style where you do thousands of different scenarios that you couldn’t possibly manage so it’s distilling that down to, ‘what of our standards do we really want to highlight?’ We know that key levers are key indicators to delivery, to safety, to behaviour, to wellbeing, we know those key levers and we make sure they are the things we are frequently asking our suppliers, our supply chain, our transport, and logistics management to be focused on. Once we know we have them distilled down and they know they are the key areas, and the other things that are important but we distill it down to a few key indicators – it’s probably a mistake that a lot of businesses make, they have far too many measures, and I deliberately say measures – you cannot have 50 key indicators.
I went to a meeting recently where somebody had 47 KPIs and you can’t possibly run a business with 47 KPIs – you can have hundreds of measures but what are your key performance criteria? We make sure our suppliers, partners, hauliers, drivers- they understand the 4 or 5 things that if they do these, the outcomes will be a continual improvement.
Simon: We’ve just published a new case study on some of the things you have done within Tarmac to manage driver safety – there’s more detail on what we are talking about here in the podcast. It shows how you have worked with your telematics partner, Masternaut, and how you used that data to deliver a really impressive 48% reduction on insurance claims in just 12 months. We are talking about data and a system like Masternaut gives you a huge amount of data to set baselines, identify trends, develop good tailored interventions and to track the performance – as you said there’s so much data available, how do you look at what are the most important metrics? Give us some of the other benefits you have achieved by focusing on the right metrics.
John: You’re right, as an organization of this size making so many vehicle journeys every day and every month, the data lake is absolutely colossal. You have to distill down to some key areas that we knew were going to reduce our collision rate. We knew we had problems with partners including our insurance but the Masternaut element really helped us to develop a dashboard – where are we with speeding? We had to reduce our speeding, especially in urban environments, we had locations geofenced, we knew who was speeding and when and why – which was important. We managed to reduce speeding by over 10% in that same period which really starts to drive down behaviour, but then there were things that people didn’t quite appreciate why we were focused on – idle time or site turnaround time and that was us getting behind the science of behavioral driving and we are into the fact about mood. Someone leaving our site, if they have sat in one of our sites waiting to load or waiting to be dispatched, the expectation is that we would turn them around and get them back on the highway in 15 to 20 minutes – obviously time is money and if they are sat there for an hour or 2 hours because we have run out of stock, frustration starts to creep in, time constraints start to creep in, so their mood and how they access the public highway where they can endanger other people, that mood and behaviour really came into focus. We achieved over an 8% reduction in site turnaround times.
Idle time – the time the vehicles are sat there being nonproductive but the engine going, it’s trying to profile these individuals and saying that’s costing fuel, and again its thinking about that whole continual improvement, professional drivers that can say ‘if I switch off my engine its better for the environment.’ Again, we saw a significant improvement in idle time and then again we could so some case studies on fuel cost savings to some of our large hauliers – that runs into thousands and thousands pounds a month, significant savings just by managing that idle time, but again it was conversations, coaching and providing some of that data to them.
I think that was the first one, and really using that data. At the same time, we invested heavily in camera technology, and we had a 50/50 bump for bump at fault insurance rate. The use of camera technology helped us to demonstrate that it wasn’t always our driver’s fault. We were able to demonstrate that by having camera technology – using that data and technology and embracing it to really continue on that journey.
Simon: With this dashboard that shows the data for all the drivers to your management team, you worked with Masternaut to create a management training programme to help them understand that data?
John: Yes, I think a lot of companies are blessed with a lot of data, and Tarmac is no different. We have so much it’s sometimes hard to say what are the things that are really going to move the dial for you – they have to be accessible and visible and user friendly and that’s something that we as a construction material company – we build great things, what we don’t do is turn data into true visible insight and I think there’s lessons there to say there are other people that are much better this than us, and using those contacts and the likes of Masternaut to develop that dashboard. The data is presented in a way that people can understand and interrogate it and use it effectively. We worked extensively with Masternaut and on a roll out programme – it’s working with the people face to face and also online to make sure those people are getting the best out of that technology and that data and insight and then putting that into action. That relationship has gone from strength to strength.
Simon: You manage such a complex set of risks – you need that outside help and obviously Masternaut provide that help with your data. What other outside help do you rely on to manage the risk?
John: Collaboration is something we all probably learn – as you go through your career, working with experts and partners, the learnings from Driving for Better Business, celebrating success by recording your case studies, working with universities and academics that really understand this stuff, you realise where your limitations are, and embracing those professionals that come from data driven, insurance companies, professionals in risk management that come and say ‘you’re focusing on the wrong things’, whether that be cars and trucks, your average car driver drives 20 miles a day from house to office, it’s important that they are well trained, you’ve got governance to check their licence and eye sight, however your trucks are doing ten times that, 200 miles a day they’re 40 tons – when a truck hits something, so really doing that professional risk management to gauge where you put your energy. You have to be able to prioritize that and use those external experts and that collaboration to help you towards your end goal.
Simon: What hurdles get in the way of good driver safety management – has there been any typical challenges that you faced that other driver risk managers might have faced as well – and how do you think driver safety managers can best deal with them?
John: I think that there are always hurdles, business priorities creep in and we are a multi-functional organization – operational teams, technical teams, distribution teams etc and they all have conflicting KPIs and conflicting priorities. I think the one thing that I am proud of and I do reiterate is part of that last mile – last mile logistics – road or rail or car and van – it plays a massive part and it normally is the customer facing piece and it’s the vehicle that leaves our site and has our final product on the back and it’s the person that turns up with a clean, compliant, legal driver and truck and represents our brand – it’s been a journey with conflicting priorities but the consistent message that we can make all the product in the world but if its sat in our site and doesn’t get to our customer – the end user – then we have not achieved our goal and certainly the revenues don’t come, so therefore when I am out with a driver or with a regional MD or a board member its really just making sure that they appreciate the value that our fleet and our drivers and our people bring to that, and I think people start to understand.
There are still some pockets where there’s a lack of awareness of that and we continue to strive to educate and inform just how important the haulage and distribution and transport and drivers are, and it’s something that has become publicly aware in the last few years – just that value – and I think more than ever we have to protect that value and make sure we look out for our drivers and our people. They have to feel part of our brand and our fabric, or the future will be a real challenge.
Simon: We’ve discussed the significant achievements including incident reduction and improvements in business performance and environmental improvements as well. To wrap up, what are the most important achievements to you and how do look to build on those in the future because risk management is a constantly evolving thing – a constant strive to improve?
John: It’s fantastic – something I’m really passionate about is data – we’ve talked about systems and technology, my key ambition now and I think it’s probably the biggest one for industry, and I talk to my colleagues across the mineral products industry, is joining that technology to make sure we recognize that predictability of some of these challenges we face with AI or embracing technology. What we are proud of – the Masternaut, the Michelin Connect, the telematics we have, a thing called One Card, where we’ve digitalized all our drivers records, we have no paper left – their competencies, their training, their experience the expiry of their CPD, that is all now digitalized on a virtual card, and is able to be validated at a point of entry into one of our sites, so that’s great. However, it’s still separate from our vehicles, and the next stage for us is really to join that technology together so that I know it’s John Anderson in our site, he’s waiting to load, he’s competent, but actually I also know that was John Anderson who was speeding 20 mins ago coming back from a delivery at a site and therefore I can intervene and he has to have a tutorial on speeding because that’s the third event etc – it’s really using the tech to our advantage to maximize the time we have with these individuals for continuing development and to automate it as much as possible. For all fleet managers, technology is out there. Some are further ahead but some are well behind but it think its about embracing that technology and making sure our suppliers are providing us with tech that is transferrable and can work with other parts because one thing we are seeing is that there is an awful lot of great stuff out there but it doesn’t communicate with each other and I think the people that can join the human being to the person to the asset to the behaviours and activities – that is the next big success and then act on on the insight and that will mean that people who come to work for anyone in a driving or construction or a vehicle – they come to work safely and they go home safely to their families at the end of the day.
Simon: Yes, and I think to have all that data together, you know what you need to do, you can show you have done it, and it’s peace of mind for all concerned.
John: Absolutely. We want people to represent our company and represent logistics across the UK – it’s a massive part of our being, and it’s so important that people are recognized and kept safe and protected and I think that technology and AI will help us on that next step of the journey
Simon: I mentioned earlier We’ve just published a new case study from Tarmac which details some of the achievements we’ve discussed, and the work you’ve done and that goes into detail on how you’ve achieved those benefits. We will put a link to that case study in the show notes so if anyone wants to read that they can see how you’ve gone about that
John, thanks very much it’s been a fascinating discussion.
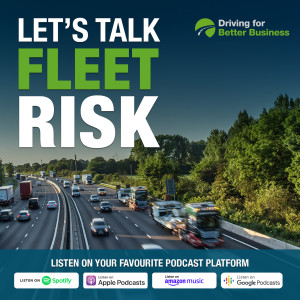
Thursday Mar 24, 2022
Could you save £56k with a Road Safety Framework?
Thursday Mar 24, 2022
Thursday Mar 24, 2022
Show notes: Could you save £56k with a Road Safety Framework?
Joining us in this episode is Dave Conway, Road Safety Manager for FM Conway.
Useful links
FM Conway Case Study
https://www.drivingforbetterbusiness.com/case-studies/business-champion/fm-conway/
Health & Safety Event – April
https://www.drivingforbetterbusiness.com/driver-safety-zone-2022/
Transcript
Simon: Welcome to Let’s Talk Fleet Risk – a podcast for those who manage drivers and their vehicles and want to reduce road risk in their organisation.
Hello and welcome to the March edition of Let’s Talk Fleet Risk.
With me today is Dave Conway who is the Integrated Management systems and road safety manager for FM Conway.
Hi Dave and welcome to the podcast
Dave: Hi Simon
Simon: That’s quite a mouthful for a job title – can you explain more about what that role entails and how you got into road safety for FM Conway.
Dave: My role is to look after the business management systems of the company – I was looking after quality and environmental systems and somewhere along the way road safety systems came along as a certifiable framework standard.
I got involved and I became beyond passionate about it – it’s now a large part of my job and we changed my job title to reflect that.
Simon: So you’re not a fleet manager or driver manager – you’re all about setting up the systems and processes that manage that road risk.
Dave: Exactly that – and I’m a great believer in systemic solutions to most problems and safe system is the key particularly with road safety. That’s really where I come from. It does mean I actually have the advantage of being independent of transport and logistical operations which enables me to take a better view on how they are doing things and come at a problem with a different viewpoint without having to worry about normal business considerations.
Simon: Just give us an idea of the size of the fleet that Conway operates – and what sort of vehicles they are
Dave: These days I think our fleet – and it’s changed a lot over the past 2 years – is around 1100 vehicles, ranging from an HGV fleet of about 400 vehicles and those HGVs could be a low loader, an articulated loader or an articulated tanker vehicle right down to 4 wheeler and 6 wheeler tippers. We then have a fleet of about 550 vans and about 80 company cars or grey fleet – and by grey fleet I’m talking about cars that are privately owned but funded by the business to do mileage on behalf of work. So that’s the breakdown. It’s a little bit of everything. If it hasn’t got wings, we tend to drive it.
Simon: Because that’s such a mixed fleet, I guess there’s a number of different people within the organisation, the people who all have an impact on road safety – fleet managers, driver managers, operations managers, transport managers for the HGVs etc. How do you work with the fact that responsibility gets shared across so many job roles – how do you ensure that everyone understands what’s their responsibility is?
Dave: The whole point of the systems, the management systems is so that everyone can follow process and procedure, regardless of whether they are running a couple of lorries or running a patch up operation on a street somewhere in town, or whether they’re running bulkers around the M25 delivering aggregates or bitumen. If everyone is working to the same management system, we can ensure consistency in terms of our output and we can ensure everyone is following the same safety standards and doing the best we can – that’s the approach.
Simon: Was that challenging – to get everyone pulling in the same direction?
Dave: It’s not so much challenging to get them pulling – no-one gets up in the morning wanting to kill people on the roads or anywhere else. However, they have different priorities – they want to get their job done. They want to be as efficient as possible with their work and so on. So, the challenge is understanding their other priorities whilst getting them to follow road safety management systems. I think as long as you can be empathetic to their other issues you can deal with it – at the end of the day the best system is one that everybody wants to follow. If it’s easy to follow they will follow it so it has to be a system that is easy to follow and works for everybody.
Simon: And is that something you asked for feedback on when you were designing these systems? How important is it to get feedback from others in the company when you build these processes?
Dave: It’s imperative. You’ll have a framework for your standards, and you’ll know what has to be in there but when you’re going to work out how you’re going to do it the people who are expert in doing it – or perhaps in not doing it – are those people on the ground. It doesn’t matter if it’s a quality system or an environmental system you have to speak to the people doing the work and say “this is what we’re trying to do – how would you do it?” Then you can come to a consensus and find the best useable methodologies and put them in place – there’s no point in putting in place something that is not going to happen anyway.
If it needs to be policed, it’s not working. If it’s the right way to do it, they are going to do it because it makes sense without policing.
Simon: So, did you get driver input into those systems as well?
Dave: Essentially, throughout. When we started establishing our 39001 system, we set up a working group and to this day it’s in place – we have people from the board, from management and drivers – drivers and supervisors – and they all sit on this committee to make sure all of their thoughts are allowed for.
Simon: So, you mentioned ISO39001 and I know you’re a big advocate for that. Why did you choose that as standard that Conway was going to embed in the business?
Dave: ISO390001 is a management system framework standard for road traffic safety. It’s been our experience and indeed the world’s experience that certified management systems work. They make a difference, there are demonstrable benefits for everybody and very few downsides.
How we got into it – it’s an interesting story. We received a letter back in 2012, Transport for London were one of our key customers and we received a letter from Sir Peter Hendy CBE who was the commissioner for Transport for London. He had commissioned a piece of research by the Transport Research Laboratory into why cycle crashes in London seemed to be dominated by construction industry vehicles. He sent us this 700-page report and it came up with a number of recommendations – and we were asked to support the recommendations. One of those was adopting a formal framework management system for your transport operations such as ISO 39001 and that was the point we embraced it.
I hadn’t heard of it – so I went and bought the book, and we did it – not realising that we would be the first. I’d spent most of my working life railing against some aspects of health and safety saying ‘why were we so worried about some aspects at work when you were more likely to die driving for work or driving to and from work?’ and all of a sudden here was a system that was supporting everything that I was saying and I embraced it with a passion – and here I am still doing that.
Simon: You were one of the first business to get ISO39001 accreditation and you did it 2012 – obviously you’ve had that in the business for close to 10 years now – so what has been the benefits to FM Conway that you can categorically say – that’s because we had that management system in place
Dave: I am always mindful of the fact that if you are going to persuade a business to adopt these systems there needs to be a business case. I really can’t overstate the business case. Within the first year of adopting the system, we found ourselves with a £56,000 reduction in our fleet insurance premium. That sum of money paid the certification for 39001 for the next 7 years. There’s your business case – if you’re running a system like that you will have less accidents. You will have less crashes, less injuries, less costs on maintenance, you’ll find that your drivers drive better and if they drive better there’s less wear and tear and less fuel usage. From a business point of view – absolutely amazing it will make money – simple as that. It will not cost you money.
There are a lot of road safety systems out there and I’m not going to quote other systems, but I can tell you from experience they will cost a small fortune. I speak to a lot of people in business, and they say we don’t have enough budget as we are a member of this other scheme and it costs us so much we can’t afford training let alone anything else.
39001 will not cost you money. Yes, there will be some costs, but I promise you you’ll get every penny back through business improvements and that’s the fundamental reason for having a system like that.
Simon: What types of vehicles you run and the number you’ve got – it’s a sizeable mixed fleet. What are the challenges in running that fleet that you think your management standards help with. If you’re not running a management standard like that what are the sorts of issues a business is going to come up against and find it difficult to manage?
Dave: With this system our biggest challenge is the drivers don’t consider themselves drivers. We have a large number of HGV drivers that we call professional drivers – these are the guys if you meet them for a drink, meet them in the street, they say ‘I am a driver’. They take a pride in that profession – ‘I’m a good driver – and I haven’t had a crash for 33 years’,they take a pride in that. What you also have is a large number of drivers who think of themselves as bricklayers, or asphalters or ground workers, who actually have a vehicle and they drive to and from work every day and at work. They may be moving themselves, their colleagues, some machines or some tools or some materials – but you ask them what they do for a living and they don’t even think about driving. They’ll take pride in their work, but they will forget about being a driver and the challenge for us is to make those guys appreciate that driving is an important part of their work and the job and they should take as much pride in being crash-free as their professional driver colleagues.
That’s the challenge – it’s one we are still working on and we are still striving to get – and we are getting better by having a management system in place as it enables them to see the successes of the professional drivers and it gives them something to embrace and be involved in as well because when you get the certification you can take the pride, and we all get it, even the pedestrians.
Simon: What have you done within the business to try and encourage that culture of professionalism among the van drivers? How do you get them to view themselves and their driving as a professional element of their role?
Dave: I think primarily it is through our certification that we can spread that pride. Internally we have some pretty good marketing approaches, we have good communication channels and every time we do something in respect of road safety we publish it.
We win awards we get prizes and so on, and we boast about them to try and encourage that sense of pride among all employees. We also have a few processes in place – stick and carrot – stick processes to maintain the standards but we much prefer using the carrot approach – we take some pride in this and I like to think that FM Conway are internationally recognised these days for the standards we set with road safety. I’ve had people come to us from South Africa to see how we do it, from Australia, New Zealand and that’s not bad going for a small private family owned business.
Simon: How do you recognise drivers – the carrot bit?
Dave: Professional drivers – it’s quite easy, we actually have a scheme we introduced several years ago. We call it the Gold Hat. When a driver reaches a certain standard, having gone so many hours without any incidents, vehicle has to be clean, they need recommendations from whoever they deliver to, they have to do a certain amount of training and they work up from a bronze to a silver to a gold hat – they get given an actual helmet in that colour which they can where in pride when they arrive on site.
Of course, you turn up and get out of your lorry with a gold helmet and everyone takes the mickey until you respectively remind them there is a very significant salary increase. Tis salary increase is self-funding – that’s the nice thing about it. We pay them more money and the scheme is self-funding because we are saving this money by not having the incidents, by having the better miles per gallon and so on. Like all good intiiatives they fund themselves.
Simon: It sounds funny and worth making a joke about but actually the ones who haven’t got the gold hat want the gold hat.
Dave: Exactly as I say it gives the guys something to take some pride in
Simon: I think that’s a key lesson for anyone trying to improve a driver culture. Better to encourage them with a carrot approach than using a stick all the time.
Dave: Totally, if you nag and poke and prod all the time, people just turn off an get worse. We found certainly with the [professional drivers, that encouragement, reward and respect make the difference. It is much harder to do with van drivers and we to have to focus a bit more on the stick, but we try to do it in a positive way and one of the things we’ve introduced is the Samsara System. It’s a live link with a telematics system that has cameras in and outward facing, there some artificial intelligence involved with the cameras so if the camera detects you are using your phone or you haven’t got your seatbelt on it sends an immediate alert to the line manager literally instantly – who can then yell through the system back to the driver “Put your seatbelt on!”
We don’t want that to be a stick, but we know the drivers know that they are being watched. Unfortunately, there will be a few people who don’t like that but those are probably the people that are of most concern.
Simon: That leads me nicely onto data – you need data to run a driver recognition scheme to know if they’re improving or need interventions. You’ve plainly got a lot of data coming from your systems. How do you manage that?
Dave; Monitoring and measuring is a fundamental requirement of any management system and we are required to do it for road safety in a positive way. So we are trying to find the good in things. We do have data logging over speeding events, harsh braking events, the system keeps track on it. We try to keep positive about it. We use it as an opportunity to talk to the drivers about their issues.
We’ve got initiatives we’ve introduced. Our E training system – e learning for drivers – and everybody who drives for us must undertake an online driver risk profiling exercise. It’s based loosely on the advanced driving test. Everyone who drives for the company, company, or grey fleet, we all have to do this driver risk profiling. It takes about 20 minutes, and it identifies those areas where you are more at risk than others.
You can come through with a set of green lights, or it might identify that you have a weakness in hazard perception or a weakness in your technical knowledge and as a result of identifying that, the system will then assign you online e-modules to undertake. So, from there we can actually focus the training on the driver’s shortcomings, and we then do a short test to check they have met the standards.
They have to repeat if they haven’t. All our drivers do that every year, so we are able to track that they are doing it and getting the training and we are also able to track their scores year on year are better. That’s the most important thing. What we are looking to do as this Samsara System takes off – and this is a wish at the moment – is identifying those people who have ongoing speeding issues. We all do it, I’ve been there, and I can remember doing a speed awareness course, and having done that I think it’s fair to say it was 8 or 9 months before I had a speeding situation again, and the courses are great but they wear off. Eventually the urgency of the situation becomes stronger in your mind than your memory of that course, and what we are trying to do at the moment is establish who the common speeders are and develop either e-training or virtual reality training modules that are equivalent to a speed awareness course and put our drivers on that so that we can tackle them before they have to go through legal process. It’s just trying to be a step ahead of the game. We are working on that at the moment.
Simon: With the driver profiling or risk assessment what’s been the driver response?
Dave: The way of the world is that all people understand they have to do occasional mandatory training. Without mentioning other systems out there, we are all aware of the most commonly used fleet management service and that has e-learning within it and drivers are required to do 2 modules a year. We found the drivers are doing the same 2 every year because they knew all the answers and could whizz through it in 2 minutes! – to be fair there’s always resistance to having to do a bit of training but people who have done the training come away from it and say – ‘actually that’s pretty good and I learned something there.’ That’s why you did that training because the system had determined that you didn’t know it and that’s’ why we’d given it to you. There are positives, there’s no more resistance to that method of e-training than any other e-training they’d ever have to do.
Simon: You talked about your professional driver recognition scheme – what other interventions or initiatives have you got or are working on to improve driver safety?
Dave: The big on at the moment alongside the Samsara system is for the professional fleet – the big trucks – we’ve had sensors on the vehicle to detect objects on the near side and far side, the blind spots and so on and we’ve had sensors fitted for some time, and what we found, certainly through an urban environment there were so many objects setting these sensors off it was not unknown for drivers to disable the system. Now I have to make it clear if we ever caught a driver disabling it we would have to have a serious word.
We know and understand this was happening because you could drive down a crowded high street and this bleeper would go off every 3 seconds so what we did – we worked hand in hand with a company called Brigade and they had a couple of our trucks and they installed computer servers in the passenger seats to gather data. They have now developed with us and are selling a system we are putting on all our trucks which is intelligent sensing. They will look at any object that is moving within the vicinity of the truck and extrapolate the route that object is going and the route we are going and if they detect a potential collision it will slam the vehicle’s brakes on. That’s going to make an enormous difference. We think that’s incredible technology and we’re very proud to be involved with it.
Simon: That sounds like a really good initiative. One of the problems with some technology is it can false alarm or trigger a number of times when it’s not necessary and that damages the driver’s trust in the system. Potentially encourages them to turn it iff. For you to develop a more intelligent system means it’s always on and there when its needed
Dave: Exactly – we’re very proud of that. We’ve developed auto stop – using it on site rather on the highway currently but for example our sweepers are all fitted with auto-stops so if an object walks behind a reversing sweeper, it will slam the brakes on, if someone moves at the back of that loading shovel the brakes are slammed on. We’re looking at how you can operate it sensibly and safely on road transport – you have to be very, very careful, you can’t just have it slamming the brakes on a truck every 10 secs – but it’s another initiative that has a lot of mileage in it.
Simon: We talked briefly about the massive insurance reduction that you had and that’s a key element in the business case for doing this, but are there any other key benefits you’ve seen as a business?
Dave: The most significant is just the sheer reduction in crashes and injuries. We monitored it – it’s one of our regular things we have to measure as part of 39001 system – and there’s no doubt that since we introduced the system the number of incidents plummeted and the number of incidents involving injury plummeted. That’s the key factor. We had a 2 year plateau at one point where we identified we had stopped improving and we looked long and hard as to why that was. We found the solutions and implemented them and continued the downward trend. In those specs that’s the big benefit. If you’re drivers are driving safely, if they have a sense iof pride that they are driving safely, then you’ll find you get the benefits in terms of costs of maintenance of that fleet as well. Our maintenance costs actually went down even though we were doing more of it. It sounds paradoxical. Because we became systemic and more controlled in our maintenance approach we found that each time it went in for maintenance there was less work to do than if you did it on an ad hoc basis.
Simon: That makes a huge difference at the end of the vehicle’s life as well – life maintenance costs are much lower…
Dave: There has to be a business case. We all take safety very, very seriously but at the end of the day if you run a business that is extremely safe, healthy but losing money the business won’t survive. There must be a sound business case for it.
Simon: You’ve got a case study on our driving for better business website which outlines that as well and the business benefits so I’ll put that in the show notes. The final point I wanted to talk about was FM Conway’s headquartered in Kent and a lot of your work is done in Kent. You take road safety seriously as the whole company. How important is the reputation for a business like yours within your local area of being a responsible transport operator.
Dave: We see ourselves as part of Kent. A very large number of our employees are residents and rate payers of Kent and we feel like we’re really involved with Kent. With corporate social responsibility and requirements, we try and support the local economy. We give work to local businesses where we can, we buy from local suppliers, and at the same time, we want to look after our colleagues, friends and our neighbours in our own county. I’m a Kent rate payer. I live in Maidstone, and I have a family and I want to know my family can go out on the roads of Kent and come home safely each day. So, it’s important to me, to all of us – Kent’s our home and we’re proud to be part of it.
Simon: Reputation is something that should concern any business especially a business like yours where you have the name plastered down the side of your vehicles – it makes a huge difference. It doesn’t take much for that reputation to be tarnished, does it?
Dave: Exactly – I had a meeting in the office the other day and we were talking about exactly that – and as I said earlier I’m very proud of the reputation Conway’s have got in terms of road traffic safety – we are internationally known for it. That puts us on a pedestal and that means we have to work that little bit harder and I’m proud to do that – it gives us the motivation and incentive.
Simon; That’s really excellent and I can see that’s paid dividends for you throughout the business. It does focus everybody’s mind. Dave, that’s been a fascinating conversation Thanks very much.
If anyone would like to quiz you or hear a little bit more you’re going to be on a panel discussion we are running at the Health and Safety Event in Birmingham at the NEC from 5th to 7th April. The panel discussion is ‘Good practice in driver safety management’ and it starts at 10.20am on the 7th April so if anyone would like to come along and hear you and a number of other driver safety managers talk about the good practice they do and how they meet the challenges I think you’ll find it a worthwhile discussion to attend. It’s in the DfBB Driver Safety Zone and there’s a link in the show notes.
Dave, thanks you very much for your time. It’s been fascinating and we really appreciate you taking the time.
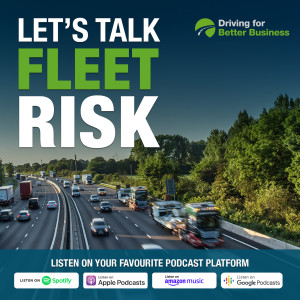
Thursday Feb 17, 2022
Van Safety Ratings - how safe are your vans?
Thursday Feb 17, 2022
Thursday Feb 17, 2022
Show notes: Van Safety Ratings - how safe are your vans?
This month's episode of the Let's Talk Fleet Risk Podcast is all about Advanced Driver Assistance Systems (or ADAS for short). ADAS covers all the collision avoidance systems and driver assistance technology that can help prevent a collision or minimise the severity in the event that the incident can't be avoided altogether. Joining us in this episode is Matthew Avery, who is the Chief Research Strategy Officer for Thatcham Research. Matthew discusses the importance and benefits of using ADAS in commercial fleets, as well as the results of Thatcham Research's latest round of safety tests on commercial vans
https://www.drivingforbetterbusiness.com/podcast/episode/van-safety-ratings-how-safe-are-your-vans/
Useful links
Thatcham Research:
https://www.thatcham.org/
Euro NCAP Commercial Van Safety Ratings
https://www.euroncap.com/en/ratings-rewards/commercial-van-ratings/
Commercial Van Safety Ratings 2020
https://www.drivingforbetterbusiness.com/articles/how-safe-are-your-vans/
New Van Safety Ratings - how safe are your vans?
https://www.drivingforbetterbusiness.com/articles/van-safety-ratings-how-safe-are-your-vans/
Transcript
Simon: Hello and welcome to the February edition of let’s talk fleet risk which, this month, is all about Advanced Driver Safety Systems, or ADAS for short.
ADAS covers all the collision avoidance systems and driver assistance technology that can help avoid a collision or minimise the severity in the event it can’t be avoided altogether. It’s a subject I’m personally fascinated by, and I’ve monitored how these systems have developed over recent years.
With me today is Matthew Avery who is the Chief Research Strategy Officer for Thatcham Research.
Hi Matthew and welcome to the podcast
Matthew: Hi Simon
Simon: Matthew – perhaps you could start by giving us a brief introduction as to why ADAS is important, how Thatcham is involved, and what your role is?
Matthew: Sure – Thatcham is a not-for-profit UK Insurance research centre and we’re members of Euro NCAP – I’m sure many of the listeners will know Euro NCAP – it’s 25 years old now and has been leading the charge to getting information to the consumer for them to buy a safer vehicle.
Since about 2014 we have really pushed the fitting of advanced driver assistance systems that help avoid the collision in the first place, and we’ve moved on from crash testing to seatbelts and airbags and the ability to avoid having the collision in the first place.
Vehicle manufacturers have been fitting technology – cameras and radars – on vehicles to detect what’s around them, respond to a potential collision threat by automatically putting brakes on and steering away from the collision. It’s very effective technology and we’re seeing it really working. We’ve now got a huge amount of standard fit in AEB technology and its reducing crashes by about 35% so it’s really good technology. It’s there not only to protect yourself but it’s also there to protect other road users and vulnerable road users. These systems will detect cyclists and pedestrians and other vehicles and [preventing a life-threatening collision. We saw this technology working so we began to broaden our scope in 2018 and looking at other vehicle types. Thatcham undertook research which showed the huge void there is between passenger cars and vans. We have a huge amount of standard fit on passenger cars – and vans from the same manufacturer have almost no technology fitted at all.
A good example is Nissan – we looked at the Nissan Duke and that has standard fit lane support systems, advanced driver systems, radars, speed limiters. Great technology – a 5-star car. When we look at the NV400 which is the Interstar at the same sort of price – absolutely no technology available at all, not even as an option and we thought there’s no reason for a manufacturer who makes the equipment, not doing that.
So, we started our first ratings in 2020 of commercial vans to highlight to the public and to fleet operators, to owner drivers and to large fleets – you must have this technology fitted. You have it on your cars, you should have it on your vans – where much of it is simply not available, choose another van. Where it is available as a cost option make sure that as an operator, you’re ticking those boxes to protect you and your driver and your brand.
Simon: So, I wanted to talk specifically today about ADAS on Vans. ADAS on cars has been developing quickly for over a decade now and we’ve reached a point where there are some fairly advanced systems available, and in order to score highly on the Euro NCAP safety ratings, most cars now have many of these systems fitted as standard. But that isn’t the case with vans, which have been much slower to adopt the technology – why is that? Why don’t they put that ADAS technology onto the vans?
Matthew: We think most of it is just down to consumer pressure and economics – manufacturers understand the power of the NCAP 5-star rating – and if you do not have 5 stars or 4 stars, you’re unlikely to appeal to a broad market. We see that with vehicle manufacturers, so they strive to get the 5-star rating, whether that’s Renault or Volvo or Mercedes Benz. Every manufacturer strives for the 5-star rating.
But as there wasn’t a similar rating for commercial vans, there’s only the regulations which did not require any ADAS fitting so manufacturers are thinking why do I need to fit it? If I can make my van cheaper and more competitive then I will do that. Some broke the mould – Mercedes was producing a lot of optional equipment and VW on their Transporter range was beginning to fit AEB as standard and we saw a market drive for that. Hence the need for the ratings to tell the consumer which van to buy.
Simon: You’ve been working with Euro NCAP to create this new safety rating system for vans so users can clearly see what systems are available and how good they are. In December 2020 you released the first set of results from tests on 19 common models of van in the UK – what did you find?
Matthew: We were shocked by what we found. Most ADAS systems aren’t fitted as standard – VW were fitting some of it as standard – but most of it including the best-selling van in the UK – Ford Transit Custom – just had none of this equipment as standard.
Some manufacturers were fitting it as an option, but there were quite a lot who weren’t even doing that – I mentioned Nissan – so we tested 19 vans and obviously a lot of these are shared – so Stellantis badge the same van in different markets, whether it’s a Fiat or a Peugeot or a Citroen, but it’s essentially the same van off the same production line.
We decided to rate in separate categories, so we have a platinum rating and there no platinum ratings, then gold – and then silver and bronze and then a not-recommended and there were too many vans that were simply not recommended. That was our first set of ratings and best performers were VW and from Ford with their large transit and the Mercedes Sprinter – those were our best performers then, but we were hoping we would see some manufacturers rising to the challenge, and this year we have.
Simon: What was the response from the vehicle manufacturers and fleet managers to those results?
Matthew: It was mixed. Vehicle manufacturers recognised this – they said we are making the right plans for the customers, and therefore there is not so much of a requirement from customers to buy this and can we really afford to make our van less competitive than another van by putting this safety equipment on?
When we talked to them, they said ‘we do have this technology – and we could fit it if there was a demand.’ We see Euro NCAP driving the demand – so the message to the fleet operators is you can’t afford to not have your vehicles on the road earning money and even after a minor collision they could be off the road being repaired – and the potential injuries for your drivers – and think about your brand reputation as well. Nobody wants to see a sign written van involved in a collision on Facebook or Twitter, so there’s lots of reason why you should be buying a van with this equipment. Our ratings make the choice clear – buy this van with this equipment and you’ve got the safest van on the market.
Simon: What’s the thinking behind the different type of safety rating to the cars – the Euro NCAP car ratings 5 star is the top whereas with the vans you’ve opted for bronze, silver, gold, platinum…
Matthew: There’s a couple of things – we wanted to separate it. We got a different message to a different audience. It’s a B2B message – we are trying to talk to fleet operators and owner drivers and they’ve probably, on their drive, they’ve got a 5 star Euro NCAP vehicle to protect themselves and their families – do they do that for their drivers?
So we’re talking to a different audience and we wanted to separate it. The other thing is this is a series of tests that we will change every couple of years so we will continue to raise the barrier and also we wanted to see this as a badge of honour so we’ve been engaging with a lot of traffic authorities like Transport for London and National Highways to inform them – they have the power to encourage the users of the roads to be driving safer vehicles so maybe you could say that we don’t want you to drive in London unless you’ve got a vehicle of a certain safety rating. Maybe you would be more likely to get a delivery contract if you have vehicles that are safer – if they’re Gold and not Bronze, you could be more likely to get that contract. We are trying to encourage a new audience to understand the benefits of driving safer vehicles.
Simon: That’s something that Driving for Better Business encourages – in one of your previous answers you mentioned about the time the vehicle is off road if there’s been an incident – while it’s repaired – and from the conversations I have with fleet managers that is one of the biggest costs / risks to the business. You can’t do business if your fleet is off the road being repaired so it’s really important that they look at this technology as it removes one of the key risks involved in running a fleet.
Matthew: That’s right and you also have to think of the driver who is injured in the incident. Hopefully they recover but they are probably not signing up to work and we know there’s a lack of delivery drivers, especially around HGVs and we understand that one of your best assets is your driver so you should be protecting that driver.
Recruiting is not so easy, so if you have safer vehicles and you’re making a point of saying – look, come and work for us because we have the safest vehicles on the market that could attract them.
What we are trying to do is make the information available A lot of fleet managers say they don’t know what to choose – manufacturers trying to flog stuff ‘but I don’t know if I need all the stuff’ so we’re helping them make that choice by saying these are the technologies that make a difference, that improve the safety of the vehicles. Why not talk to your insurer – does that mean your fleet premiums are reduced? Worth talking to them as well.
Simon: What are the technologies – what are some of the most common you want to see adopted?
Matthew: The most important is AEB – autonomous emergency braking – using a radar or a camera or a combination of both using a concept called sensor fusion to identify if the driver is responding and if they don’t put the brakes on automatically, so stopping front into rear crashes – the most common urban crashes. It also prevents accidents with pedestrians and cyclists as well. AEB is one of the most important technologies.
The second most important is probably out of lane support systems – a lot of crashes occur because drivers are momentarily distracted and their vehicle crosses over a white line either into another car or runs into a tree or crosses over the centre line – all crashes you want to avoid so we look at lane support technologies, as well as simple seat belt reminder warnings. Very powerful encouragement to put a safety belt on. Too many commercial vehicle drivers are not wearing safety belt even though it’s a legal requirement.
Also, things like speed limiters – a lot of people see this as big brother controlling your speed but it’s also extremely helpful. People really see the benefit of controlling their speed. Having a reminder to tell you this is a 30, 40 or 50 speed limit. Most of us want to stick to the speed limits and having a reminder is really helpful. It helps you keep a clean licence as well.
Simon: I sometimes hear people being a bit disparaging of these systems, probably through lack of understanding that drivers can get lazy, and complacency sets in. Is that a valid concern?
Matthew: Probably but we don’t see it in the statistics. When we look at the efficacy of these systems in the market, vehicles that have this technology have fewer crashes than those that don’t. Period. So why wouldn’t you want this technology?
Simon: So, the reason we’re talking today is that you’re about to release the second set of results for the van tests. Have things improved?
Matthew: Yes, they have. I’m pleased to say Simon, they have improved. Probably the standout star is the Fiat Ducato. That is the very first platinum rated van. That is the safest van that we’ve ever tested – it’s a fairly regular van – not high end – but we’re very pleased that Fiat have made the provision to put the technology on the vehicle. It doesn’t come as standard, you have to tick the box, but at least the Stellantis Group that own Fiat are making that technology available. So that’s the first platinum rated van.
We also see some movement on the Ford Transit Custom – the UK’s best-selling van has got a gold rating – it was silver before – and really, the most disappointing is probably Nissan with their Interstar – which was formerly the NV400 which was our worst performer and gets a ‘not recommended’ rating. Nissan doesn’t even see fit to fit the technology as an option. If you check their equivalent price passenger cars like a Duke or a Qashqai, they have the technology as standard. We voted the Qashqai the ‘What Car’ safety car of the year because it had so much good technology in a value package. So, Nissan know how to do this, but when it comes to vans, they seem to ignore the customer so I suggest maybe van operators might want to look elsewhere.
Simon: You mentioned that a lot of the vans in previous years tests, similar to what you said about Nissan – the technology wasn’t even available as an option. You tested 19 vans last year – have you seen that manufacturers are more willing to offer this technology now?
Matthew: Yes – we’re seeing Renault and Ford using more technology and their ratings increasing so our first step is to make the technology available and a sneak peak on our next ratings – we will be putting our requirements even higher and will be expecting manufacturers to fit a lot of this technology as standard. We will continue to raise the bar and encourage fitting as standard as they do for passenger cars.
Very good ratings so far and we’re pleased to see a significant increase especially as van sales continue to rise. Let’s see a corresponding rise in the safety ratings of those vans. The manufacturers are on notice that we will expect to see the technology flitted as standard in the future.
Simon: What about the different technologies themselves? Do you see variations on the capabilities in an AEB system or a lane keeping system across different manufacturers for example?
Matthew: Yes, we see some differences. The Fiat Ducato’s AEB system was very good for cyclists, pedestrians, car to car, whereas some of the other systems such as Renault are less sensitive – they work with cars but not always pedestrians and cyclists so we do see some differences in performance and that’s why it is so important that we have these grades. It’s not a tick box – you either have AEB or not – it’s also how good is the system.
One of the most important technologies we are beginning to see fitted would be the Drive monitoring systems. Again, it sounds like spies in the cab but this technology, which is very new even to passenger cars, we are not seeing on vans yet – but it’s monitoring the drivers status to makes sure the driver is not drowsy and whether the driver is paying attention. There’s an awful lot for a van driver to do now. They have very quick turn round between drops and its all too easy to be distracted looking at mobile phones to see where your next drop is, so that technology which brings the drivers eyes back to the road all the time is vitally important to increase safety.
Simon: You mentioned about fleet managers to take these safety systems into consideration when they are acquiring their vans, I guess whether they are leasing or buying. One of the things we want to do is to encourage much wider fit across vans as that then helps the technology to filter through to the secondhand market. That technology then becomes available to others. What should fleet managers be saying to their leasing companies or manufacturers to encourage this to be fitted as standard or at a lower cost? Can fleet managers put pressure on the manufacturers to work harder at this?
Matthew: I think fleet managers have a role to play. If you’re looking at a new fleet of vans you can look at some of the brands like VW who are fitting this technology as standard and make a choice there as opposed to other brands. I would urge fleet managers to look at our ratings. If you want a standard fit system, then some manufacturers are making vans with standard tech, and I think that a fleet manager making the point that ‘we’ve decided on these new vans for our fleets because they tick all the boxes because we want a safe fleet’ – that’s making a very important statement. Manufacturers understand the power of that, and their product can continue to be competitive so I think there is a huge bargaining case that fleet operators can make – and the fleet managers – in saying ‘I am not buying your vehicles unless you put this equipment on, and you make it standard.’
Simon: One of the things I noticed from the results this year as well as last year, there’s a huge spread from top to bottom – they do seem to have shifted slightly further upwards as we have our first platinum van, and in the previous results there were 5 ‘not recommended’, but there’s only one this year. There’s still some improvement, but that huge spread of results is still a concern isn’t it. Do you expect the rest of the manufacturers top follow Fiat’s lead and put some more effort into this now?
Matthew: Yes, we would. As you said, we have one coveted Platinum manufactured, 7 Silver, 6 Bronze and 4 Golds so manufacturers are beginning to respond. One of the things behind this is that there is a new European regulation called the General Safety Regulation – GSR2 – that stipulates new vans going on sale this year will have to have some of this technology fitted as standard, so a European directive is forcing manufacturers to do this and by 2024 all manufacturers will have to fit some of this technology.
So you might ask why we are doing what we are doing. Any regulation like that tends to work at a fairly low level so while manufacturers will be forced to fit the tech it won’t be a high performing system so what we will be moving towards once we get manufacturers engaged is making it standard fit and then really pushing the performance to avoid manufacturers just fitting the minimum requirements to pass the regulation – actually fitting high performing systems. You won’t get Gold or Platinum unless you’ve got a system that way outperforms the regulatory requirements plus there are several things in our ratings that aren’t yet required in the regulations, so we are going as ever above and beyond where the regulations lie – even in 2025.
Simon: Fantastic. We are publishing this podcast just after the official test results are released so where can our listeners go to find out more about the test results and see where the vans they commonly purchase sit in that league table?
Matthew: Euroncap.com – they can see all the ratings there. You can find a link to that on the Thatcham Research website. The other useful provision on the EuroNCAP website is you can drill down into that and it will show you the availability on each market so we cover EU27 plus 1 now and we show the ratings across all of the EU states. You’ll be able to look at the UK and say what’s available on our van because it is different between countries. And we do have a reasonably high level in the UK and we’re much better than say France or Italy – so it’s doubly impressive that Fiat have decided to make this equipment available as an optional fit – and I would urge people to look at a Platinum van – look at a Fiat Ducato.
Simon: Fantastic. We’ll put links to that in the show notes. Matthew, thank you for being our guest today and I look forward to seeing what the response will be to these latest results.
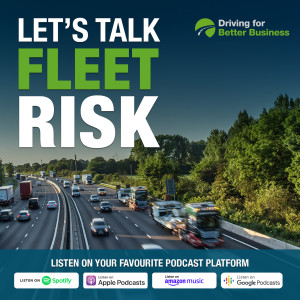
Friday Jan 07, 2022
Safe loading - where do fleet operators get it wrong?
Friday Jan 07, 2022
Friday Jan 07, 2022
Show notes: Safe Loading
Welcome to the first podcast of 2022. The Driving for Better Business Campaign is focussing on loading issues this month, so we asked Nina Day from the HSE to join us for this episode. Nina has worked for the HSE for 21 years. She’s a chartered mechanical engineer and a dangerous goods safety advisor specialising in road and workplace transport.
https://www.linkedin.com/in/ninaday/
Useful links
Driving for Better Business Resource Library
Driving a van: weight limits and loading
https://www.drivingforbetterbusiness.com/resources/search-results/?res=Driving+a+van%3A+weight+limits+and+loading&id=9896
Load security: good practice
https://www.drivingforbetterbusiness.com/resources/search-results/?res=Load+securing%3A+good+practice&id=9896
Load security: roles and responsibilities
https://www.drivingforbetterbusiness.com/resources/search-results/?res=Load+securing%3A+roles+and+responsibilities&id=9896
Load securing: vehicle operator guidance
https://www.drivingforbetterbusiness.com/resources/search-results/?res=Load+securing%3A+vehicle+operator+guidance&id=9896
Load security: consequences of poor load security
https://www.drivingforbetterbusiness.com/resources/search-results/?res=Load+security%3A+consequences+of+poor+load+security&id=9896
Load security: how DVSA enforces the rules
https://www.drivingforbetterbusiness.com/resources/search-results/?res=Load+security%3A+how+DVSA+enforces+the+rules&id=9896
Ratchet straps: What you need to know
https://www.drivingforbetterbusiness.com/resources/search-results/?res=Ratchet+straps%3A+What+you+need+to+know&id=9896
Securing loads on flatbed vehicles
https://www.drivingforbetterbusiness.com/resources/search-results/?res=Securing+loads+on+flatbed+vehicles&id=9896
HSE Website
https://www.hse.gov.uk/
HSE Driving and Riding Safely for Work guidance
https://www.hse.gov.uk/roadsafety/
Van Driver Toolkit
Safe Loading
https://vandrivertoolkit.co.uk/
Loading: Know Your Limits
https://vandrivertoolkit.co.uk/
Transcript
Simon: Welcome to Let’s Talk Fleet Risk – a podcast for those who manage drivers
and their vehicles and want to reduce road risk in their organisation.
Welcome to the first podcast of 2022. The Driving for Better Business Campaign is focussing on loading issues this month, so we asked Nina Day from the HSE to join us for this episode. Nina has worked for the HSE for 21 years, she’s a chartered mechanical engineer and a dangerous goods safety advisor specialising in road and workplace transport.
(transition)
Simon: Hi Nina – welcome to the podcast.
Nina: Thanks for inviting me – it’s great to be here.
Simon: Now, Nina, I know that safe loading is right at the top of HSE’s list when it comes to work related road safety. At DfBB we focus on commercial vehicles and HGVs tend to be heavily regulated but vans less so. What regulations apply to each vehicle category in respect of load safety?
Nina: Well, the regulations are the same regardless of the size of the vehicle, so it doesn’t matter if it’s an HGV or a passenger car – it’s the same legislation. We have section 48 of the road traffic act, regulation 100 of the constructions use regulations and they both say the load has to be secured to prevent someone being injured. There’s also the workplace safety aspect. If you’re an employer or you’re a self-employed person whose work covers other people which covers a lot of people in transport, then you have legal responsibilities under the safe and healthy at work act and legislation to protect anyone who works for you, and also anyone who could be at risk because of your work, so that’s wide ranging. These are 2 separate areas of law, but they do overlap. The responsibilities overlap quite a lot and it’s the same regardless of the size of vehicle.
Simon: So, what are the common problems that you see where fleet operators get this wrong and you see unsafe loads? When the regulations are ignored, what do you see on the roads?
Nina: The fundamental problem where an incident has happened – usually a fatality or a serious injury – it’s a lack of risk assessment or the risk assessment is so inadequate it may as well not have existed. That’s something I’ve seen in the vast majority in load shift incidents I’ve worked on in the last 15 years. There are a lot of misconceptions on risk assessments – but it doesn’t have to be bureaucratic and time consuming. It’s just thinking through what you do, what could go wrong and what how to stop someone getting hurt if it does go wrong. HSE provides a lot of free guidance on our website. If you haven’t thought things through, the chances of everything else being right are actually quite low. All the other issues we see follow on from not having the risk assessment right. It’s also a legal requirement so if you’re an employer or self-employed, you do need to have a risk assessment.
The other issues I see a lot are people using the wrong load securing for the load they are carrying. Load securing equipment that is damaged or old and worn and not fit for purpose, or not using enough load securing. There’s no specific method – it’s up to you depending on the load you are carrying and the vehicles you are using. Whatever you do you must secure the entire weight forward and half the weight to the sides and rear. That is a minimum and if you secure to that level the load should stay where it is in an emergency stop, if you have to swerve to avoid a child, anything like that – the load should stay where it is.
A big issue at the moment is open vehicles, whether that smaller drop side type up to big tippers because people don’t appreciate that loads can move upwards and when that happens loads can be thrown off the vehicle.
About 5 years ago a lady was killed when a piece of work equipment that weighted about 60kg bounced out the transit pickup and struck her as she and her husband were walking on the pavement. That item should have been secured and it wasn’t. It bounced up so high it cleared the height of the sides and came of the vehicle.
Only last year a man was killed when a chunk of stone that only weighed 8kg bounced of the vehicle and came thorough his car windscreen,. He was driving with his wife and grandchildren and killed instantly. No one sets out to kill anyone like that. I think one of the most difficult things I’ve ever read over the last 15 years in looking at load shift incidents was in a statement from a driver who had been involved in an incident and he started off by saying ‘I never set out to kill anyone’. But if you’re operating an open vehicle you need to make sure that load is properly sheeted, properly tied down, properly covered, big items tied down so they can’t bounce out. Don’t assume that the sides by themselves will stop the load from coming out.
Now, I think the last point I want to make is that when you’re loading a vehicle you’ve got to make sure it’s not overloaded. Its very easy to do with vans and smaller vehicles. Just be aware of what your vehicle is rated for and what you can put in it. When I’m out with the police and the DVSA I see a lot of overloaded vehicles. If you overload the vehicle if you don’t distribute the load evenly across the load bed that will affect the handling of the vehicle. It might increase the braking distances or make it more likely to roll over so it’s really important to think about how you load it and make sure you’re not overloading it.
Simon: Brilliant, so to dig in a little bit deeper into a couple of those points. We were talking about items in an open back LCV or a tipper truck that can jump out. You could go over a pothole or a speed bump, or anything – I’ve seen that happen as well. One of the things we’ve quite often seen come out of compliance checks, trucks where all the big stuff is secured properly, so plainly they know what they are doing, but then they throw a few last minute items in the back, a bucket of bolts, a generator, a shovel. They know what they’re doing but they just haven’t done it with the last bits. One of the worst things we saw were a couple of power saws with uncovered blades which could do some serious damage if they jumped out. Is that something you see? That they know what they’re doing but they just get it wrong at the last minute and throw a few bits in – it’s that attention to detail that everything is secured?
Nina: Absolutely. I think there is an assumption that if something is very small it might not move and if it does come off, what’s the danger? The reality is it doesn’t have to be a big item. If it’s flying off at 50 mph it could very easily kill a pedestrian or a cyclist, or go through a windscreen and kill a driver. It doesn’t matter how big the item is. I see it all the time. The larger items are secured really well. I see this with plant equipment on low loaders, The plant equipment is secured fantastically but any unused chains or straps are just left on the load bed and there’s nothing then to stop it coming of the side and going into oncoming traffic and I actually helped a police force investigate a fatality where that happened. A chain slipped off the side and went into oncoming traffic and killed a driver. So whatever it is, even if it’s a really small light item you need to make sure that it can’t come off. If you have lots of small items, the easiest way to secure them – put them in a box or covered container and strap that down That’s the easy way to do it – or just sheet the whole load bed and then nothing bounces out.
Simon: Because if you think that even a small item once it has momentum can do some serious damage can’t it. The other thing we were talking about was weight distribution on the bed of the truck or LCV and making sure it’s all strapped down properly but what happens if you’ve got drivers who are doing multiple drops, so you could start the day with a load where the centre of gravity is evenly spread across the axles but then as they make drops you could end up with the centre of gravity moving over one axle or it becomes too high and theres; a risk of overturning. Do you see that?
Nina: On many occasions – I think very often drivers can be frustrated about that because they know it’s a issue. What I would say is that multi drops are generally not unplanned. The company knows it is happening and this really comes back to the risk assessment. At that stage if you’re a company delivering to lots of different sites, part of your risk assessment should be how are we ging to make sure the vehicle is safe once bits of the load comes off. That might mean talking to the delivery site and making arrangements for it to be rearranged for the driver. I think it can be quite frustrating for drivers and I’ve spoke to a lot of drivers at road side checks who bring up this point. It’s left to them to negotiate with the site to get their vehicle reloaded an sometimes that’s refused. Sites say if we reload you we are taking responsibility. It’s not from a legal perspective, particularly accurate, but it’s quite a pervasive issue I think. It’s very difficult because then you’ve got a dangerous vehicle going out on to the public highway. It is a company responsibility when you load a vehicle doing multi drops -you need to think about how it’s going to stay safe once parts of the load are coming off.
Simon: Let’s look at responsibility a little more then. Typically, if someone is driving a vehicle that’s falling foul of some road traffic act regulation – overloaded, shed load, even poor driving or vehicle maintenance, your typical expectation is that the driver would carry the can for that but when we are talking about risk assessing a load., how much involvement does a driver have there? I’ve heard stories where the driver has no awareness, he gets in the cab and is told to do the drops. Where does responsibility lie for ensuring safe load – presumably across a number of people?
Nina: Shared responsibility. Everybody in the transport chain – driver, transport operator, whoever put it on the vehicle – the consigner. From an HSE perspective we would consider the consigner to be the primary duty holder but everybody has some responsibility which is not the same as culpability.
While the driver may have some responsibility for the vehicle when its on the road, the driver is not necessarily culpable for the way its been loaded, the way the load has been tied down or not. There can be really good reasons for keeping drivers away from loading. If it’s a big busy site, you don’t want drivers run over by vehicles or forklift trucks. One of the risk assessments may be to keep the driver safe in a lorry park or in a safe waiting area and that’s fine, not a problem, but if that’s the route the site is going down then they should be able to give the driver some assurance that the vehicle or trailer has been loaded properly and the load has been secured so the driver is confident he is going out with a safe load
In terms of enforcement, I think historically there was a temptation that it would all land on the driver and particularly at the roadside. That’s not necessarily fair. The way that enforcement works now, it’s very much if the driver is not felt to be culpable, the driver has not had the opportunity to make the load safe, or involved in loading, they will not get a fixed penalty ticket or points on their licence. The vehicle may be prohibited from onward travel until its made safe but it will not come personally to the driver, and it’s the same with an incident. In the 15 years I’ve been looking at load shift incidents I can think of one where the driver alone was culpable. One incident in 15 years out of a few hundred so generally speaking when you have a load shift incident the culpability is actually somewhere else in the transport chain and that’s what we would look at as part of the investigation
Simon: So that would be the point that you or one of your colleagues from HSE would go and start an investigation as to whether the other people in the business have done the risk assessment, and whether correct procedures are in place to ensure safe loading and all of that kind of stuff?
Nina: There are different ways this can work. If something happens on the road, the police have primacy for that. They can ask for help or they may do the investigation alone. They will also look at other parties in the transport chain as that shared responsibility is in the road traffic act. It is in section 48 – it says the driver and anyone who causes or permits a vehicle to be on the road are responsible for its safety so that’s already in law for the police to look at that shared responsibility. Certainly, we do work with the police very closely on load security incidents. We can do a joint investigation, or we can support their investigation and that does work quite well.
Simon: There was an incident earlier in May 2021, there was a video going round that had been released of a gentleman and his wife driving out to lunch in his Tesla and as he approached a right hand bend a truck came round the other way – a flat bed truck with a load of concrete blocks on it – the driver of the truck took the corner too fast and the concrete was not secured and it slid onto the top of the Tesla, and it was only the safety structure that saved the driver and his wife because it pretty much trashed the rest of the car. I think you saw the clip at the time – that’s an example of how loads can shift if they are not fitted on properly. I don’t know whether anyone was found culpable for that?
Nina: I know the video and I think it surprised people – when loads move they do tend to move very suddenly. It can be quite difficult to imagine a heavy load of steel or concrete that had to be craned on or fork lifted on ever coming off. When you are standing next to a parked lorry looking at a load like that you wouldn’t think it would move so quickly and suddenly. It does happen and I’ve seen it many times. I think these incidents often go under the radar and people are not aware of the scale of it These days more more and more people have dash cams so we are seeing more footage of this kind of incident, but I think seeing the reality of it does raise awareness that these things do happen. The potential consequences are horrendous.
Simon: It really was quite staggering to watch – we’ve got a link to the clip on our website so we’ll put a link in the show notes if anyone hasn’t seen it – so they can see what a scary experience that was.
Coming back to the one of the things you said earlier, about common problems relating to overloading. I’ve seen some quite comical pictures almost of vehicles that are so obviously overloaded, no one who saw that vehicle could be in any doubt that it was overloaded, but I guess they are the exception, but you do see a lot of vehicles where they are overloaded to a lesser extent, and it’s maybe not obvious, but they are significantly overloaded as a safety issue because its harming the handling and braking characteristics of the vehicle.
What sort of good practice should businesses be looking at to ensure they are not overloaded? Is it just a matter of training?
Nina: One of the key things is to be really sure of what your vehicle is rated for – I know that sounds silly but it does come up a lot at road side checks. I don’t see as much overloading with the heavy goods vehicles. We tend to see it with the vans and the smaller pick up types of vehicles and sometimes people don’t know what the vehicle is rated for or they have misunderstood what it’s rated for. I was out once with the police and a 3.5 tonne body was brought in. The driver got out and said ‘its fine, its fine – its rated for 3.5 tonnes and I’ve only got 3 tonnes in the back…’- there’s nothing malicious there, not deliberately trying to evade the law it’s just a misunderstanding of what the rating actually means. That would be my key point. Be aware of what your vehicle is actually rated for – it’s not always obvious so just check what that’s rated for under UK regulations. Check with the manufacturer if you need to. Look at what you’re actually putting into it. I think with the van, most people would probably do this. You’ve got a van, you’ve got a cubic space. The temptation is to get the most in there you possibly can. So just be aware of what’s actually going in there and that weight as it’s very easy to go over – to overload it – and the fines for overloading can add up quite quickly.
Simon: I know one of the conversations I’ve had a number of times relating to multi drop couriers and home delivery services is that with everybody working from home and not going out socialising typically people are ordering a lot more alcohol for instance – wine and beers – and so a lot of the couriers are finding that they are delivering that to homes where it would have previously been less heavy cardboard boxes, it’s now a lot of liquid which is far heavier than they are used to for a given sized box. We’ve heard stories where there’s lots of overloaded vans, I’ve got that much space I can fill the space but they’re finding what’s going in is a lot heavier than a couple of years ago
Nina: This comes back again to the idea that it’s not just on the driver here. If you’re a business that is sending out goods for delivery to home addresses, and they’re heavier loads you might need to revisit your systems, your risk assessment actually – do we have to change things. That’s the key thing with risk assessments – it’s not something you do once and never look at it again, it’s a constant process because things do change. As we’ve seen with the pandemic people are working at home, ordering more things online. Things are changing and businesses need to change to make sure they are not straying into territory that’s putting people at risk.
Simon: You mentioned the guy that put 3 tonnes into the back of a 3.5-ton lorry – it’s such a safety critical error as it makes such an impact as to how the vehicle will handle. One of the things I’ve become aware of is in the vehicle recovery market where companies are recovering vehicles because people are not paying loans etc and recovering them on the back of a 3.5 tonne LCV rather than a larger vehicle. The payload on one of those is probably around a tonne if that so there’s very few cars – a very tiny super mini – you could put on the back of a 3.5 tonne flatbed, yet you hear stories of larger vehicles so that could easily be overweight. What’s the impact of someone doing that and what would be the likely consequences in terms of an investigation afterwards?
Nina: if an incident did happen and it happened because of the way the vehicle was loaded, if it happens on the road the police take the lead in investigating that and they may involve HSE or a local authority to look at the management system side. If it happens in the workplace then either we or a local authority would investigate. In any incident relating to load, the general approach would be to look at every party in the transport chain – who has done what, have people thought about what they’re doing, just to go back to what I said about risk assessment. Often people think there’s a lot of paperwork and it’s very much a box ticking exercise. You don’t need to – you need a common-sense system in your business to manage safety and that’s what we’re looking for. So the best case scenario in an incident is that you are able to produce evidence of your system. Unfortunately, the incidents I’ve been involved in, that very often hasn’t happened. It’s come out afterwards that there really is no system. There’s been a great reliance n the drivers making the best of things and doing the best they can. Drivers often make a reasonable job of it, and they keep things running but it doesn’t mean the system is fundamentally safe and that’s what we look for.
Simon: When you talk about the transport chain does that include sub-contractors? What if there’s an incident with a vehicle and the vehicle operator / owner have fallen foul of some of these things we’ve been talking about – but that transport movement was commissioned by a client and the client hasn’t checked to see whether the sub-contractor has got policies and procedures and knowledge to do it – does the client have any culpability?
Nina: It’s fair to say no 2 incidents are the same – it depends on who is felt to be in control of the transport operations and I’m sorry I can’t give you a nice black and white answer, but it is individual to the incident and the actual transport arrangements. It may be that you have a company who are the controller mind if you like and who are directing how things are done, but are not directly involved in the transport and that’s something that would come out in the investigation, because there is a duty under health and safety law to cooperate and communicate with other companies you are working with –
Simon: So they would have a responsibility to be involved and ensure any sub-contractors knew how to do this properly and ensure they use competent people?
Nina: Indeed – don’t just assume what was okay 10 years ago is still okay now – times change, technology changes. It may be there is a better way of doing things. I know since I started 15years, equipment, new trailers have come onto the market. It’s worth looking round and getting advice and seeing if there’s a better way of doing things.
Simon: What sort of resources are available to employers and fleet operators and their staff so they understand their responsibilities for risk assessments and safe loading?
Nina: I mentioned the HSE website earlier – we have risk assessment and workplace transport and load security resources on looking after visiting drivers, this is all free to access. You can also ask us a question directly. I know sometimes people are nervous because they think they are going to end up on a list for inspection – that’s not true at all. You can use the form on the website or ring us up. We will answer your question and you won’t end up on a list for inspection just because you’ve asked a question.
You can get guidance on load security from DVSA, from the gov uk site, there is all the DFT guidance, safety of loads on vehicles – those are both free to access and download. You can also get some really good advice from National Highways particularly for the smaller pick up type bodies – they have a really good leaflet on how to load safely. But it’s also worth getting in touch with industry associations – if you’re a member they will very often have their own resources. If you’re in a union, speak to the union. I will say for drivers if you have a concern about the way things are being done – if you’re in a union speak to the union rep. if you’re not you can come to HSE directly and raise concerns with us. If there’s something you think is dangerous and putting you or other people at risk, we do look at those concerns and we do act on them
Simon: Nina that’s fantastic – we will put links to all those resources in the show notes so if you want to download any of those we have sign posts on the DFBB website to help you download and access those resources
It’s been a a fascinating discussion, thanks so much for coming on the podcast Nina.
Nina: It’s been a pleasure thank-you
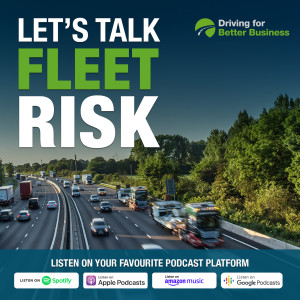
Thursday Dec 09, 2021
Driver Fatigue: Not just a tick box
Thursday Dec 09, 2021
Thursday Dec 09, 2021
Show notes
I’m joined today by fatigue expert Dr Paul Jackson of Fresh Air Training
Paul is a Chartered Psychologist specialising in human performance and has assisted safety-critical organisations to implement fatigue risk management systems for over 20 years in a career that has also included positions as
- Research Manager at the Department for Transport responsible for looking at impairment resulting from fatigue, drugs and alcohol
- Visiting Lecturer in driver fatigue at Cranfield University
- Head of Impairment Research at TRL
Paul was an expert witness in last year’s landmark legal case, in which the Office of Rail and Road successfully prosecuted an employer for health and safety breaches, as a result of two of its employees being killed in a road traffic collision where fatigue was identified as the primary cause.
This successful criminal prosecution demonstrated that having policies and procedures on fatigue management is not enough.
In this podcast, Paul and I discuss:
- The events leading up to the crash,
- What the company did wrong and why it was prosecuted,
- The key lessons for employers to take away from this case,
- And where to start when looking at fatigue management.
https://www.drivingforbetterbusiness.com/podcast/episode/driver-fatigue-not-just-a-tick-box/
Useful links
Driving for Better Business Article on the case.
https://www.drivingforbetterbusiness.com/articles/company-found-guilty-after-driver-fatigue-death/
Driving for Better Business ‘fitness to drive’ resources
ORR press release on guilty verdict
https://www.orr.gov.uk/search-news/contractor-renown-consultants-ltd-guilty-after-two-died
ORR press release on sentencing
https://www.orr.gov.uk/search-news/contractor-renown-consultants-fined-ps450k
Transcript
Simon: Welcome to Let’s Talk Fleet Risk - a podcast for those who manage drivers and their vehicles, and want to reduce road risk in their organisation. I’m joined today by fatigue expert Dr Paul Jackson, of Fresh Air Training. Paul is a chartered psychologist, specialising in human performance, and has assisted safety critical organisations to implement fatigue risk management systems for over 20 years in a career that has also included positions as Research Manager at the Department for Transport, where he was responsible for looking at impairment resulting from fatigue, drugs and alcohol; Visiting Lecturer in driver fatigue at Cranfield University; and as Head of Impairment Research at TRL. Paul was an expert witness in last year’s landmark legal case, in which the Office of Rail and Road successfully prosecuted an employer for health and safety breaches, as a result of two of its employees being killed in a road traffic collision where fatigue was identified as the primary cause. The successful criminal prosecution demonstrated that having policies and procedures on fatigue management is not enough. In this podcast, Paul and I discuss the events leading up to the crash; what the company did wrong and why it was prosecuted; the key lessons for employers to take away from this case; and where to start when looking at fatigue management.
(transition)
Simon: Hi Paul - welcome to the podcast. Paul: Good afternoon.
Simon: We’re going to talk today about a double fatality due to driver fatigue that ultimately lead to the successful prosecution of the company that employed the two who died. Now, Zac Payne was a trainee welder who was just 20 years old. He worked for a company called Renown Consultants, and was driving a company van at the time of the crash. He had his 48 year old colleague, Michael Morris, sat next to him in the front of the van. Now, Paul, you were involved in that case as an expert witness. The outcome should have significant implications for employers. I was wondering if perhaps you could start by just giving us an outline of the events that led up to this particular crash.
Paul: Sure. So, the events that led to the renowned prosecution occurred on the night of the 18-19 June, back in 2013. In the early hours of Wednesday 19 June, the two welders you mentioned, Zac Payne and Michael Morris, were killed when their van - the van they were travelling in - crashed into an articulated lorry, which had been parked in a lay-by on the A1. They had been on their way back to Doncaster, after a night shift in Stevenage, in Hertfordshire. The previous day, the day before the incident - so that’s Tuesday 18 June - Zac Payne had driven another Renown crew up to a place to Alnmouth in Northumberland. He’d left Doncaster, where the depot was, at 4:15 in the morning, and that crew arrived at around 7:30 in the morning, and waited for the job to start. But for various reasons, that job was cancelled, and so Zac Payne then drove the crew back to Doncaster, arriving at around 3 in the afternoon. In the meantime, an urgent job had come in which required two more welders for a job near Stevenage - a place called Langley Junction. And that job was going to happen on the 18-19 June - so that Tuesday night/Wednesday morning.
The company, Renown, allocated Michael Morris as the senior welder. And the only person they could find as the assistant was Zac Payne. So, they were allocated to do the job, and they set off for Langley Junction at around 7:15 in the evening. Mr Morris was driving, and they arrived at Langley Junction at around 9:45 in the evening. They had to wait to take possession of the railway, and that happened from around 11:15. They completed their tasks, and then set off on their journey home, just after 3:30 in the morning. And this time it was Zac Payne who was driving. At around 5:30 in the morning, the van had been travelling north on the A1, and straight off the carriageway to its near side, and into a lay-by where the articulated lorry was parked. Their van hit the articulated lorry and unfortunately, tragically, both Michael Morris and Zac Payne were killed. At the time of that collision, Zac Payne - the driver - had been up for around 26 hours.
Simon: So, in this case, the prosecution was brought by the Office of Rail and Road, rather than the Health and Safety Executive. but Renown were still prosecuted under the Health and Safety at Work Act. So, could you just explain what it was they were actually prosecuted for please?
Paul: They were prosecuted on three breaches of health and safety regulations; the 1974 Health and Safety at Work Act, and the 1992 Managing the Safety of the Workforce Act. So, the first breach was failure to manage the fatigue of their workforce. Secondly, for exposing employees and non-employees to the risk of injury arising out of fatigue. And thirdly, for failing to make a suitable and sufficient risk assessment before these two particular employees were sent out on that night shift.
Simon: So, fatigue was clearly identified in this case as the primary cause of these Fatalities, but, in the rail industry, fatigue is well known as a risk because they’ve got a large workforce that are often operating at night because that’s when the tracks are free for maintenance or they’re doing shift work. So what went wrong in this case on the management side? Did they have a system for managing fatigue?
Paul: They had procedures. They had, I suppose, the rudimentary elements of a fatigue management system. Certainly they were not without procedures. The procedures they had included a policy - a fatigue management policy, procedures for assessing the risks associated with fatigue, and particularly the procedure to authorise excess hours; so where somebody was being requested to work longer hours than normal, they had an authorisation form that was meant to be completed as a result of the risk assessment. What went wrong was that the company didn’t follow its own fatigue management procedures. In addition to that, they didn’t comply with the working time limits for safety critical work - such as welding - which require that there should be a minimum rest period of 12 hours between booking off from a turn of duty to booking on for the next duty. In addition to that, they didn’t conduct a sufficient and suitable risk assessment - particularly of the fatigue of Zac Payne, who as I mentioned had been awake for a considerable length of time even before starting this job.
Simon: You see a broad spread of attitudes, shall we say, among companies towards risk. Where, at one end you have a total disregard – don’t care, not interested in managing risk, just doesn’t register and all they care about is running the business, up to the other end, where managing risk is central to the business, and nothing happens unless it’s done the correct way. In the middle, you often have people who maybe want to do the right thing but maybe haven’t got the time or are under pressure, or they don’t have the experience to do it properly. Are you able to say where Renown’s management fitted on that scale?
Paul: Yes, and I think perhaps it’s better for me to refer to the sentencing remarks of the judge in this particular case - His Honour Judge Godsmark. In his sentencing remarks he said that he was satisfied that if Renown had followed their fatigue management procedures - if they’d implemented them - that would have amounted to all that was reasonably practicable to negate the risk of injury through fatigue – but it was in the implementation of those procedures that Renown failed their employees. He went on to say that the operations managers at Doncaster knew what they were supposed to do in managing the safety of their employees - particularly in relation to fatigue - but, only lip service was paid to these systems.
He concluded that there was a wilful blindness of operations managers when it came to considerations of fatigue - particularly in relation to driving times and the distances to and from jobs. He also said that evidence from the employees - other Renown employees - suggested that safety briefings could be perfunctory, and concentrated on getting ticks in boxes. I think one of the other damning elements of the case was that although Renown was subject to annual audits from an independent third party, those audits didn’t shine a light on the way in which those procedures - those stated procedures - were actually being applied, or not applied. And as a consequence, Renown failed to prove that they were doing all that was reasonably practicable to implement those written fatigue procedures. So, you have a weight of evidence there which suggests that this is a box ticking exercise. The management didn’t really take fatigue seriously. And it probably suggests issues with the culture of the organisation. I think this is not confined to Renown, who weren’t a bad company and are still operating today, so clearly are doing a lot right, but I think many organisations fail on this level whereby they may well have procedures written, on a whole range of safety issues, but they need to be collecting the data, documenting their actions, so that they can demonstrate to the regulator that they are following those procedures.
Simon: That attitude that you said was prevalent among the operations managers - I’m assuming that was just below board level - was that attitude reflected with the senior management of the business?
Paul: Very much so. The operations management were specifically referred to by the judge, and it’s clear that that same attitude even persisted during the trial. I think one of the comments that the judge made was that, despite this incident having occurred in 2013 and changes having been made subsequently to procedures and particularly to Renown’s policy on driver fatigue, that wasn’t the change that was needed. The paperwork was adequate, he said; it was the implementation that needed to be looked at. Essentially, what was needed was a change in the culture of the senior management team.
Simon: I think you referred to it as a ‘tick box culture’ before, and that kind of thing
is not just restricted to driver fatigue, is it? We see that for many companies, for many different elements of risk management as well. There was one thing that struck me when you were outlining the events running up to the incident - while Zac Payne was driving at the time of the crash, you said Michael Morris - his colleague - was driving to that second job that Zac was on. So was that Michael Morris’ first shift, or had he also been at work for as long as Zac?
Paul: No, he’d rested that day. He hadn’t worked in the same way that Zac had. He had already been scheduled to work that night shift so he was probably better prepared, or had the opportunity to be better prepared. I think one of the big problems with Zac Payne’s situation was he was given very little notice of this night duty - and clearly not enough time to prepare adequately to be sufficiently rested before undertaking that night duty.
Simon: And clearly he would have been potentially at risk carrying out the work because he was fatigued - but I was intrigued because Michael Morris was plainly insured on the van if he drove to the job, so I was wondering why Michael Morris didn’t drive on the way home, as Zac must have been clearly overtired.
Paul: Yes. I think there was an informal arrangement where one drove on the way, and one drove on the way back. That seemed to have been fairly standard practice within the organisation at the time.
Simon: One of the reasons Zac took on this extra shift, I believe, is that Renown was also found guilty of creating a staff payment structure that encouraged its employees to take on extra shifts - so he took on that extra shift because he would have been allowed to earn extra money. I think you mentioned that they had a policy around the authorisation of excess hours, so presumably, one of the management processes should have prevented him saying yes to that shift, or more to the point should have prevented him being asked in the first place.
Paul: Well I think the policy you’re alluding to really is their zero hours contract. So, there was an incentive to work fatigued, because of course when they weren’t working they weren’t getting paid. Obviously that creates an incentive to take any shifts that are given to you - particularly for a young man like Zac who was keen to keep in with his employers. He was keen to get his welding qualification. He’d been given indication that he would be put on the next welder’s course if he did as he was asked, so he was very keen to, A, take on extra duties; and B, to do everything he could to keep his management happy. Unfortunately the side effect of that is there’s an incentive to hide fatigue and to continue working even when fatigue might be an issue.
Simon: The management failures weren’t just around fatigue - there were also problems around the driver checks I think, weren’t there? Because Zac wasn’t really insured to be driving the van in the first place I don’t think.
Paul: Yes, their insurance policy required drivers to be over 25 to be covered by the insurance. Zac was only 20. Clearly he was not insured, or covered by the insurance. But that seemed to be quite endemic within the organisation - to the extent that on the previous duty, the early duty, where Zac drove up to Northumberland, none of the crew in that vehicle were over 25 and qualified to drive. So clearly there was no possibility that they could follow their procedures, or their insurance policy procedures, for that particularly duty, so it was definitely a frequent occurrence, even though at the trial I think the management maintained that they were unaware of that. I think the general view of the court was that that was probably not the case.
Simon: I’m sure I read as well that the investigating authorities had interviewed a number of other staff within the business that backed up that that was a regular occurrence.
Paul: Yes, absolutely.
Simon: Because that’s something I’ve brought up many times when I’ve been discussing the possibility of a prosecution. One of the things that employers need to be aware of is that the investigating authorities aren’t just investigating your policies and procedures, and what you did; they will go and interview other people in the company, and they’ll typically find some of the most disaffected employees who will tell it like it is. So there’s very little opportunity for you to try and cover up something that actually is widespread practice within the business.
Paul: And I think that’s very much the case with this particular investigation. As I said, this investigation lasted 7 years. During that time, the ORR interviewed I think about 70 or 80 different witnesses. The witness bundle runs to nearly 2000 pages. It was clearly a very in depth investigation. It didn’t just stop with witnesses from within the organisation, but also witnesses from other organisations, people who had been on site at the time. There were also things like phone records, hotel records to see whether any employees were being given hotels after night duties - which was, again, one of their written mitigations for managing fatigue. A whole range of data was collected and analysed, so yes, a very, very thorough investigation.
Simon: There was one bit about this case that particularly staggered me, and you mentioned in your introduction at the start that the original crash happened in June 2013. So the fact that the length of time for the investigation and prosecution was a full 7 years for that to be concluded because, I think, the verdict was announced in March 2020, and then the sentencing was in June. So, a full 7 years under the stress of that investigation and prosecution. Did you see what kind of effect that had on those who were involved in the incident?
Paul: To a certain extent, yes. I mean, you can only imagine the stress, the anxiety, the impact on every aspect of your psychology, if you like, that having a case like that hanging over your head for that length of time must have had on those individuals. I think it was evident at the trial - this was clearly something that had been going on for so long the impact was inevitably going to be quite profound, in terms of its impact on their stress levels, if nothing else.
But of course, all of that pails in significance by comparison with the impact on the families of those individuals who were killed tragically. But yes, it’s clear that the prosecution and the consequences of prosecution aren’t limited to the fines that were imposed upon the company. I think the longer term impact on the management of that company would be equally damaging I suppose - it would be difficult to cope with.
Simon: Yes, absolutely. And without trying to minimise the stress and trauma that the families went through - as a business owners it’s got to be an incentive to do this properly; to manage it properly. Now I’m sure we’ve got many employers listening to the podcast now who know that fatigue is an issue in their business - and maybe we’ve got some where it isn’t recognised perhaps to the level it should be. What do you think are the main takeaways for employers from this particular incident?
Paul: There are a few. I think maybe the first starting point is, as you said, employers who recognise that fatigue is affecting their business - can you articulate that? What is it that you do that might be contributing to fatigue? What are the fatigue related hazards to the safety of your employees? That’s the starting point. Is it because you’re operating at night, like this company were? You do long hours? Whatever it might be, identifying the contributors to fatigue is the starting point for me. Secondly, thinking about what are the worst case scenarios - what could go wrong if an employee was exposed to fatigue? And then once you’ve identified those beginning and end points, if you like, the next step is to be able to understand and identify what controls you have in place to prevent that contributor to fatigue resulting in an employee experiencing fatigue. So do you have sufficient controls in place for each potential contributor? How robust are those controls? How likely are they to be subject to degradation over time? Then, in the worst case scenario where an individual does experience fatigue, where your controls have failed, what mitigations do you have in place to prevent that fatigue resulting in the worst case scenario - for example a traffic accident. I think only when you can answer those questions adequately - as an employer, as the accountable manager of an organisation – it’s only then you can sleep safely and recognise that you’re doing everything you can that is reasonably practicable to manage and negate the risk of injury through fatigue. But the starting point for all of that is getting the culture right within the organisation. I think one of the main failings of the Renown business at the time of this incident was that lack of safety culture around fatigue. It wasn’t recognised in the way it should be, and, as the judge said, paying lip service to the systems they had written. That’s where the main failings are, and that’s where I think an organisation really needs to start it’s more effective management of fatigue.
Simon: The fact that they had the policies shows that obviously they were clearly aware fatigue was an issue that needed to be managed, and that they didn’t follow those policies, led to the accident. Obviously, if you weren’t aware fatigue was a problem, you could have still had a similar accident. The fact that they demonstrated they knew that it was an issue by creating the policies – that’s almost worse isn’t it? Because it makes the failure a wilful failure.
Paul: Yes I can see where you’re going with that. Very much so. As that judge referred to - a wilful blindness of the operations managers when it came to considerations of fatigue. So they recognised that what they were doing was likely to cause, or contribute to, fatigue, but, other matters got in the way of the effective management of that issue. I think, even though they had procedures in place, it was clear that the operations staff, at the Doncaster depot at least, didn’t really understand how to use those procedures - which all contributed to that idea that this was just ticking a box to say ‘yes, we’ve got procedures in place, they’re compliant with the regulations’ But of course, as you say, the fact that they recognised fatigue as an issue, and had stated how they managed it, and then failed to do so, was doubly damning I suppose is one way of looking at it.
Simon: You mentioned when we were talking about the staff contract structure, and the incentivisation of working extra hours, that they were on zero hours contracts. Is that a common thing in other sectors, for instance, where it could cause driver fatigue to be an issue?
Paul: I think in the last few years there’s been increased recognition of the prevalence of what they call the gig economy which essentially is founded on multiple zero hours contracts. Having several different jobs with different employers - but each of those being a zero hours contract. I think yes it is more prevalent than it used to be. Whether it’s more prevalent in certain industries than others... probably in the road transport sector - certainly delivery drivers, for example. I know there have been cases where organisations have been challenged on the nature of their contracts with their employees - partly on the basis that it’s not an effective management of the health and safety of those individuals who, for all intents and purposes, are under the control of that employers - so, yes, I think it’s certainly increased in prevalence in recent times. And I don’t think it’s a healthy situation as this case really demonstrates, tragically.
Simon: Yes. I wanted to ask you a final question just about fatigue more broadly, I Guess, and that’s how conscious do employers need to be around staff personal Situations - where, it might not be obvious that the job itself is causing fatigue, but if the job involves driving, and circumstances in the employee’s personal life might cause fatigue in another way. They might have sleep apnoea, they might have young children that keep them awake at night, they might have other anxieties or worries that cause them mental strain in other ways and prevent them sleeping properly. How much do employers need to take account of those kinds of issues?
Paul: Tricky isn’t it. I think there’s only so much that an organisation can do, in terms of managing fatigue within the business, and there is always going to be a requirement for the individual to take some responsibility for their personal fitness for duty. It’s clear that fatigue doesn’t just originate from either one source or the other. Clearly there are contributors to fatigue associated with the operational practices, as was the case with this particular company. There will also be a whole range of contributors to fatigue, potentially, which originate in the personal life of the individual; their lifestyle, their health, social activities, etcetera, etcetera. The conventional approach to addressing that potential problem or weakness in the system is to ensure that the culture is right around honest and open reporting. So, we often talk in fatigue management circles about the importance of shared responsibility. The employer has a responsibility to provide time off and adequate time to enable the individuals to have obtained sufficient sleep. The equivalent responsibility for the individual is to use that time to obtain adequate sleep. Secondly, the employer has the responsibility to take seriously any reports of fatigue that are brought to their attention, and to put in place the mechanisms, if you like, or framework - be it a form, or a reporting system - which gives individuals the opportunity to come forward and hold their hands up and say ‘sorry, I’m too fatigued’ but by the same token, the individuals within the organisation - the employees - have the equivalent responsibility to do so; to hold their hands up and say ‘personal factors outside of work may be contributing to my fatigue’. That all requires, for many organisations, quite a significant change in culture. I can well believe that some of the people listening to this podcast will think ‘well that’s never going to happen in my organisation - people don’t hold their hands up and say they’re fatigued’;. If that’s the case, if you truly believe that, then you certainly need to do something to try and address that issue because that’s always going to be a barrier. If you don’t have the information, and people don’t feel comfortable to come forward with that information, then how do you know what your fatigue risk truly is?
Simon: Paul, thank you for sharing your insights and expertise with us. If anyone has any questions on fatigue management, are you happy for them to get in touch with you?
Paul: Yes, it’s been a pleasure to talk to you - and if anyone does have any questions that haven’t been addressed by this particular podcast, by all means contact me - either via my website - freshairtraining.co.uk, or by email - paul@freshairtraining.co.uk. You can also find me on LinkedIn.
Simon: Fantastic. Paul, it’s been a pleasure to have you on the show - thank you very much.
Paul: Thanks very much indeed. Cheers Simon.
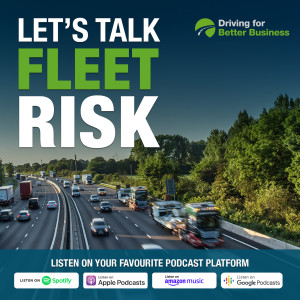
Tuesday Nov 09, 2021
Driver wellbeing: How reward breeds success
Tuesday Nov 09, 2021
Tuesday Nov 09, 2021
Show notes
Welcome to this edition of Let's Talk Fleet Risk - a podcast for those who manage drivers and their vehicles, and want to reduce road risk in their organisation.
In this episode, Simon Turner, Campaign Manager for Driving for Better Business, is joined by Phil Hitchen, the Managing Director of Belle Vue Manchester - award-winning and quality-branded transport provider.
Phil and Simon discuss
- The importance of driver personality to good service and maintaining high standards across multiple locations
- Reducing driver stress, and recognising and rewarding good driver performance
- Why awards are so important to the business, helping to drive a culture of consistent high standards
https://www.drivingforbetterbusiness.com/podcast/episode/driver-wellbeing-how-rewards-breed-success/
Useful Links:
Belle Vue website
10 Mistakes to avoid when procuring school transport
Transcript
Simon: Welcome to Let’s Talk Fleet Risk – a podcast for those who manage drivers and their vehicles, and who want to reduce road risk in their organisation. I’m Simon Turner and I’m the campaign manager for Driving for Better Business – and my guest in this episode is Phil Hitchen, who’s the Managing Director of Belle Vue Manchester, an award winning and quality branded transport provider. In this episode, Phil and I discuss the importance of driver personality to good service and maintaining high standards across multiple locations. We talk about reducing driver stress and recognising and rewarding good driver performance. And finally, we look at why awards are so importance to the business, helping to drive a culture of consistent high standards.
(transition)
Simon: Hi Phil, and welcome to the podcast.
Phil: Morning Simon! Pleasure to be here.
Simon: Phil, most businesses only have to worry about the risks to their drivers or other road users, yet your vehicles are generally full of customers as well, which could be quite a daunting challenge. What’s your view on work-related road risk at Belle Vue?
Phil: I think from a transport point of view… if you train your people right, your drivers right, do your safety checks and health and safety announcements, and show passengers what to do in the event of an emergency… I think if that comes second nature and ingrained in the way they just reel it off every job… I think if your maintenance team follow the operational guidelines and procedures, it just runs like clockwork and it’s no fluke that your insurance claims records stay low, your MOT pass rates stay at 100%, when it comes to vehicle inspections… the traffic commission and DVSA alike with their inspections every 6 weeks; we like to do ours every 4 weeks because we operate from an ethos of ‘a stitch in time saves nine’ and it keeps the fleet running at optimum level.
Simon: So what’s the biggest challenge you think you face in running a safe service for customers?
Phil: I think in 2019/20/21, it’s evident there’s a shortage of PCV and HGV drivers in the UK. I think we’re quite proactive on training drivers to basically meet a service charter which requires things (to be a little higher standard) than the average. We have to recruit more numbers now to get the quality of driver we want, whereas 10 years ago they’d come flooding through the doors, you’ve got a nice fleet, you pay good wages, you’re a nice company to work for an youd look after your team. Right now, after a pandemic, coach drivers have gone into other trades… there is a huge shortage.
So for me, the biggest challenge at the moment, which has gone on for about 3 or 4 years since the CPC really kicked in, where elder drivers retired and didn’t want to go through the CPC, and there’s a shortage of young drivers coming through, so I think the biggest challenge to the industry and certainly our business is getting the right calibre of drivers through the door in the first instance.
Simon: And how do you then look at ensuring they’ve got the capabilities and the right attitude? How much effort do you put into driver assessment and training to ensure that they do deliver the level of service that you expect from them all?
Phil: We probably do a lot more than your average company, and we probably do some things differently than some of the top companies in the UK. My philosophy is we recruit personalities and we teach them to drive later. So, what we do is, straight from the offer and application form, we measure people’s personalities. Once that’s done, they do a driving assessment. If they get offered the position, they then do anything that could start from a 1 day to 5 day induction training, depending on experience. About 10 years ago, I knew our business could do a lot better, and I knew our drivers could drive better. I knew that as a business, the directors and the board and the management team could perform better – so we decided to put tracking systems on all of our fleet; what that did was tell us how drivers accelerate, how they brake and how they corner. We decided to use a system called Traffilog, because I perceive that to be the market leading system – National Express favoured that. Operators who work for National Express only seem to use the basics that National Express wanted to use, whereas we used everything. We literally drove peak performance driving, and then when we’d done that and we were saving copious amounts of fuel, which was about £63,000 per annum, we decided to use this personality tool to measure people so that we could get them to respond to passengers and give better service.
Simon: So with the tracking system then, that would typically give you a lot of data on driver behaviour – how much time do you spend analysing that data and how do you use that to improve performance and improve the service?
Phil: So, any bus or coach operation has key performance indicators. The accounts department, they have certain KPIs that they look at – the bank balance, the direct costs, the sales, the overhead. They’re always looking at their dashboard of figures. In operations – in tracking our drivers let’s say – we have people in compliance, whether it’s watching CCTV or watching the tracking system, we have people watching the idling times. Basically, it’s on a scoring system, and if you visualise a scoring system from 0-200… when we first set out, we had drivers averaging between 40 and 100, so 0-20 would be really good, it’s what we call “The A Team”. 20-50 is good, and 50-100 I class as average. Over 100-150 is inefficient, and 150-200 is technically dangerous. We made it company policy to get all our drivers under 50. When we achieved that, we had 1 or 2 stragglers, lurking around 60-70. And some of these guys were experienced, we’re not talking about somebody who’s just passed the PCV licence and is a bit of a novice. Just regarding accelerating, braking, and cornering. Imagine a coach going down a main road at 30mph, about a quarter of a mile away they see the lights turn to red – an educated driver will take his foot off the accelerator, cruise down to about 20mph, they’ll see the lights change and he’ll put his foot to feather the accelerator and he’ll build that back up. And if you imagine you saw a chart where people are driving erratically, it would go up in the air and then drop down when he brakes, it would go like a zig-zag. When you get tracking education into drivers, those sharp points become smooth ridges, like a wave on the ocean. And I had drivers saying to me, “…what are you going to teach me about coach driving – I’ve been driving 20 years”, and I say – this is science, let’s just go with it. They say “…well the girl who’s monitoring it doesn’t even have a PCV licence – what’s she going to teach me?”. And then suddenly they did get all these notifications about over-accelerating, cornering incorrectly, and braking. We educated them – we’d send supervisors and operations managers out with them. And literally in a 2 month period we’d get all our team under 50. Then we got a league table; we have a bus league, a school bus league, and a coach league. And what we do is we have £300 worth of prizes, so basically the top performing driver gets £150 a month, the second and third placed drivers get £75 each. And it’s not because of the money, but it’s a bit like soldiers – you’ve got Dad’s Army, the regular army, the paratroopers, the SAS… Coach drivers are the same. They want to be in the SAS. They want to walk in their driver room knowing they’re a top performing driver. When we got the league tables going – and it wasn’t just for the money, although that did influence people – they would compete with their colleagues to get the top scores, and that’s driving with a 0 score. That means no events, no harsh braking, no over-accelerating, and those KPIs that our compliance team see, if they go above the 20 which we class as ‘The A Team’, what happens is, when people are driving efficiently, they drive safer, passengers get a comfier ride, there are less roadside RTAs, there are more vehicles on the road rather than in the garage being repaired. If you invest in that system, and you invest in the right supervisors and compliance team tracking, drivers do perform better. When they don’t, you know there’s education/training to get them where they should be. And if they haven’t got the desire to improve, you replace them.
Simon: I love the idea of the SAS of coach drivers. How have the drivers responded to that then? That seems like a fairly comprehensive driver recognition system, where you really are rewarding the right attitude and good behaviours. How did the drivers respond to that?
Phil: Well in the early days, if you look at coach driving over the 60s and the 70s, throughout the North-West of England for example, you had streets and streets of neighbours getting on a coach and going on a jolly to Blackpool for a week. Then the motor car came along, and drivers used to have this situation with the passengers, where they’d go on holiday and, while everyone’s having their dinner, they’d swap all the pyjamas of everyone on the first floor with those on the second floor, and cause chaos. Once they were out of that coach depot, they were very much a law unto themselves.
Fast forward to 2020, a driver’s now got a tracking system monitoring his every move, any operations manager’s mobile phone can see where any fleet vehicle is at any time, they can see whether the engine’s on or off, we have live CCTV on the vehicles to see what’s moving – so they’re very much controlled. When that came in, over the last 10 years, drivers were a little bit negative towards it. But once they realised that if they have an insurance claim against them that’s not their fault, it’s non-fault, we have 8 cameras all over the vehicle – 4 inside, 4 outside – those cameras support the evidence of the story of the drivers, and we have non-fault claims. At first drivers were a little bit negative, but in this day and age now we live in a transparent world, it’s just second nature to the driver, they take it on board and they quite like it really. They’ve got cameras there covering them, operations can support them if there were any hostile events on the road, which are very rare. We do live in a busy society now on the motorway, and local and regional roads – you do get unsavoury behaviour sometimes with motorists, and I think drivers feel a bit more secure now.
Simon: Yeah. It’s quite clear that you put a lot of effort into this, and I know that on the website you’ve got not only your safety policy but also your core values on safety. So what do those core values mean to you, as the managing director of that business?
Phil: What they mean to me is, if I went to a restaurant and I see a nice menu, and there’s a star with the core values about where the food is sourced from, how the chef is passionate about cooking certain ingredients in a certain way to give a certain flavour… that would really enthuse me to buy into that brand. Everybody has favourite brands – I buy clothes from Hugo Boss, or there are certain Italian restaurants that I frequent in Manchester. But when it comes to coach travel, there are people who pick up the phone once a year and want a jolly to the seaside, or to the Christmas party. There are other corporate organisations and schools and education centres that have passengers moving every day. With our core values, it’s not something we’re playing at; it’s our livelihoods, it’s something we’ve done for decades. We like people to understand our ethos on coach travel, and our ethos is every school trip should be safe – and not only that, it should be fun-packed, it should be a carefree adventure. I remember when I was about 10 years of age, I had a coach trip to Chatsworth House. I haven’t got a clue who the driver was or who the company was, I just went to a nice stately home. If somebody said to me that they went on a Belle Vue coach trip and they didn’t know the driver’s name, and they didn’t know it was our company I would be horrified, because we like our drivers to present to the passengers in a certain way. I think values are very important for any business.
Simon: You operate obviously across the country, from London right up to Scotland, and I think you operate throughout Europe as well, and you subcontract to other companies and you’ve got a really broad operation geographically – and I think you’ve grown quite rapidly too. So how do you ensure those standards are maintained across all the locations in which you operate?
Phil: If we do a deal with a customer, or we take on a new member of staff, or we subcontract to another company, we like to communicate well, and the deal has to work for both parties.
So, if we take on a new member of staff, we promise to pay every month on the 7th of the month, we promise to pay bonuses for peak performance, and there are other perks and benefits which I won’t bore you with that we promise to do. What we expect in return in that contract of employment is to be smart and well-groomed, to carry out safety checks, to act in the company’s best interests, and to be on best performance day-in, day-out. When it comes to dealing with subcontractors – so we operate from Manchester and the North-West of England, we operate all around the UK, mainly in the North-West, a little bit in London and around certain cities like Glasgow and Edinburgh, we do tours into Europe – all those tours into Europe are not from operating centres in Europe. They’re all trips that have come from the North-West of England, or in the Midlands, or occasionally down South. They’ll go all around Europe, and they are for tour operators or private hire groups, with the strategic partners we have located. So we have an array of operators, and I think about 8-10 years ago, somebody phoned me up and said “I want 5 coaches in London, I want you to do it”, and we didn’t have any fleet in London, so we started getting industry partners with our same ethos of quality, vehicle presentation, maintenance standards, we’d obtained their licences and insurance, their operational guidelines, we’d get them to sign paperwork… we’d do a cross-deal, so if they represent us in London, we represent them in Manchester, and then that happened with other cities. Occasionally – very, very occasionally – you might get a slight poor performance with one operator, and we’ll drop that operator. Normally we just marry up with drivers who want to work with our ethos, and other subcontractors who work on that. We promise to pay at the rate agreed, and have a working relationship that works, really, and is reciprocated.
Simon: I know you subcontract work out to partner companies as you said, but equally you’re effectively a subcontractor to some corporate clients. One of the things I wanted to delve a little bit deeper into was, where you’re an outsourced provider for a business, and that business effectively still has a duty of care to its staff – you might be running a minibus shuttle service for a business, or a coach trip to take business directors or clients out somewhere – so your client has a duty of care to ensure the safety of all those staff, and that the transport service is provided in accordance with the law, it’s done safely, the vehicles are all well-maintained and all of that. So how importantly do you think your clients take that, and how importantly do you take that responsibility to ensure that you can prove to that client, that business customer, that you do all of these things to such a high standard?
Phil: Well, everything we do is audited, whether it’s vehicle presentation, driver service, driver presentation, driving skills, etcetera. And they can leave comments; they can leave negative comments for improvement, they can leave praise, they can give an overall driver summary in a testimonial. So when we get those after-sales reports round the table every Friday afternoon, tens and tens of after-sales forms, sometimes hundreds – we will look at those, and we’re not looking for the 10/10 and the glowing testimonial, although that’s very good; we can use those testimonials on websites. What we’re looking for is somebody who says something like “everything was 10/10, the service was great, however the coach was 5 minutes late”. We think it’s really important to get a great start on any journey; if you’re late, if there’s a breakdown, if the customer’s frustrated… It takes hours out of that day to pull that back. And it can be pulled back, but our philosophy, just like preventive maintenance, is to look at the after-sales forms, look where we can improve the business, and it’s evolving all of the time.
Simon: I find that bit really interesting actually, because fatigue and stress and things like that are significant contributors to collisions and such like, and actually what you’re doing – you called it preventive maintenance – what you’re actually doing is removing some of that stress from the drivers, because they’re all more prepared, aren’t they? They’re in earlier, they know what to expect – it’s taken a lot of that stress away from drivers, which just makes them calmer and less likely to have an accident, doesn’t it?
Phil: Very much so. If you look at a pyramid of an organisation – your board of directors at the top, then the senior management, then the operations team, then your garage staff, and then your valeters, and then your drivers – in any normal organisation you would see the pyramid with the directors at the top and the drivers at the bottom. Really, you need to reverse that so the drivers are at the top and the directors are at the bottom. Because really, drivers are out there battling through traffic; congestion these days is far more serious than it was say 30 years ago. Drivers need every resource to be able to execute their job to a high standard. They feed things back, and I think listening to the drivers and changing things means people feel more valued. I think in terms of taking details, and being thorough on bookings, rather than the driver being a bit blind, it all makes for a calmer day. It’s all down to the planning really Simon.
Simon: Yeah. And you clearly do that well. I know you’ve got your safety policies on the website as well, you’re proud of those, and they clearly work extremely well in practice. And you’ve got a whole load of UK coach awards as a company. You’ve been awarded ‘Best Coach Company’, ‘Best Business Coach Company’, ‘Best Business’, ‘Best Customer Service’, Innovation Awards… and it’s not just the business, it’s individual staff as well – your staff have received industry recognition. Not just the drivers, you’ve got engineers, customer service staff, office staff – you’ve obviously created a really fantastic culture in the business where everybody in Belle Vue follows the values of the business – they mean as much to the individual staff as they do to you. So, has that translated into benefits for the business, in terms of higher performance, lower crashes, lower costs? What are the business benefits from operating the business as you do?
Phil: What the benefits are… we have a very, very strong people culture. Around 7 years ago we invested in 5 brand new Mercedes-Benz Turismo coaches. And Evobus – who we bought them off, the Mercedes-Benz dealership – invited us over to Turkey to watch the coaches being made. And then they invited us to Petronas Formula 1 team, and we had a tour around one of their factories. My co-director, who’s a bit of a petrolhead, saw Nico Rosberg’s Formula 1 racing car – I wasn’t particularly interested in that… But what I was interested in was the ethos of Mercedes-Benz Formula 1 team. When you see Nico Rosberg shake the champagne when he wins a race, everybody thinks he’s the man. What they don’t realise is, when he goes in the pit, there are 12 engineers there, one with an earpiece. And in that earpiece are 42 engineers back in Northampton with a computer connected to some part of that car. So the moral of the story is, it’s a team game. Coach driving is exactly the same. If we’re going to get a 10/10 performance during a coach tour or corporate trip, those mechanics have to be on board, the operators have to be on board, the accounts and compliance and HR teams… they’re all part of that. So, we really get across a great team ethos. We want people who are passionate about what they do. When we look at industry awards, we think “who are the best performing people in our business?”. We encourage our people to compete, because what we like them to do is have a taste of success. There are all sorts of awards for Unsung Heroes – someone who goes around, does a great job, and never gets any thanks or recognition, a bit like a defender or midfielder in a football team, not the guy who gets all the goals. We like to decorate our people, and once they get a taste of that, success breeds success. And when somebody sees that we’re working with the UK Coach Driver of the Year, they all want a taste of that. The only reason we do that, is that after that accolade, they have to maintain a high standard of service – customer service – on that coach. And that just brings more business in.
Simon: I was going to ask that actually – delivering to that level, and the staff culture, and the awards – that requires a lot of effort as a team to put all that together. Does that actually translate into a high level of business? Does it make a difference when you’re pitching for work?
Phil: Of course it makes a difference. If you were going to hire a coach to transfer your staff or guests or clients, and you’ve got a company who not only invest in modern vehicles but have got all these safety standards and KPIs that are quite impressive, and they’ve got a team who clearly demonstrate that the customer is number one and king, and they communicate more effectively – I don’t know any other passenger transport business in England who teaches their drivers to communicate with their passengers in that way.
Simon: I think it’s one of the biggest benefits I see, when it’s clear that a company is operating at that level it really does translate into a better impression with the potential clients, it helps retain business, it helps win new business, so I think you’ve proved that again. You’ve been running Belle Vue in its current guise now for around 25 years I think. So I’ve got a final question for you, which is what’s the most important thing you’ve learnt around managing drivers and managing vehicles in that time?
Phil: I think it’s learning to light people’s fire really. People have different passions – I mean if you want somebody to perform at a certain level you need to find their switch that turns them into someone who’s got desire. Desire to perform. The biggest thing I see across the industry, when you go to coach parks, you go to Alton Towers – you see different levels of desire of drivers. Some are there just for the sake of it; some are there just to earn a living; some drivers will do the minimum they have to do to get through the day; and others just exude customer service. So, I think it’s finding people’s desire, trying to line up their personal goals, and wants and needs for their aspirations, and lining them up with the company’s business model. And when that happens, fantastic things start to happen. We’ve won Engineer of the Year in our garage, we’ve had other people take silver and bronze, and I’m talking young people here, not people who have been experienced for decades. We’ve had Unsung Heroes in operations, we’ve had UK Coach Driver of the Year, 2 years ago. I think for me, the biggest thing I’ve learnt about the business is nothing mechanical or operational. It’s about human behaviour, and how we can get the peak performing teams.
Simon: Fantastic final pearl of wisdom, thank you Phil. Thank you so much for being on the show and sharing your insights with us, really appreciate it.
Phil: You’re very welcome Simon, I wish you all the best.
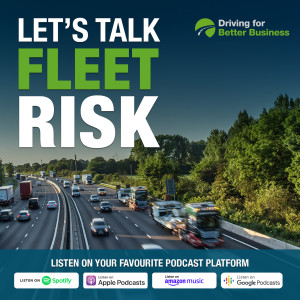
Saturday Oct 09, 2021
NHS Hospital transport: a gigantic challenge
Saturday Oct 09, 2021
Saturday Oct 09, 2021
Show notes
My guest in this episode is David Malone who is the Transport and Travel Advisor for The Newcastle upon Tyne Hospitals NHS Foundation Trust.
His responsibilities include setting and implementing the strategic direction for all hospital managed transport as well as all delivery transport movements to and from site.
This includes not just fleet vehicles, vans, pool cars and grey fleet but also car parking, park and ride, passenger transport services, taxis and couriers.
David also chairs two Best Practice Groups for the NHS National Performance Advisory Group - one for Transport and Logistics, and the second for car parking, sustainable transport and active travel policy.
In this podcast I’m going to be talking to David about how he manages such a wide range of transport activities including a grey fleet of almost five thousand and the challenges of driver communication with such a large workforce. We discuss the challenges around ensuring outsourced transport providers meet their legal obligations to manage road risk, and we look at how the Trust’s transport activities will need to develop in the future to meet their zero-carbon ambitions.
Useful Links:
Newcastle upon Tyne Hospitals declare climate emergency
https://www.newcastle-hospitals.nhs.uk/about/ambitions/climate-emergency/
DfBB resources for Grey Fleet
https://www.drivingforbetterbusiness.com/resources/search-results/?section=312&category=Grey%20Fleet
Transcript
Simon: Welcome to Let's Talk Fleet Risk - a podcast for those who manage drivers and their vehicles, and who want to reduce road risk in their organisation. I'm Simon Turner, and I'm the campaign manager for Driving for Better Business. And my guest for this episode is David Malone, who's the transport and travel advisor for the Newcastle-Upon-Tyne Hospitals NHS Foundation Trust. His responsibilities include setting and implementing the strategic direction for all hospital-managed transport, as well as all delivery transport movements to and from site. This includes not just fleet vehicles - vans, pool cars and grey fleet - but also car parking, park and ride, passenger transport services, taxis and couriers. David also chairs two Best Practice groups for the NHS National Performance Advisory Group; one on transport and logistics, and the second for car parking, sustainable transport and active travel policy. In this podcast, I'm going to be talking to David about how he manages such a wide range of transport activities - including a grey fleet of almost 5000 - and the challenges of communication with such a large workforce. We discuss the challenges around ensuring outsourced transport providers meet their legal obligations to manage road risk, and we look at how the Trust's transport activities will need to develop in the future to meet their zero carbon ambitions.
(transition)
Simon: Hi David. Welcome to the podcast.
David: Thank you very much. Thanks for having me on.
Simon: David - hospital trusts have a huge range of transport activities as part of their routine business operations. I was hoping you could start by just telling us a little bit more about your role - how many vehicles you're responsible for, and the different types of staff mobility and transport movements that a trust like yours needs to manage.
David: Okay, so in terms of the size of our organisation - we're one of the largest trusts in the United Kingdom, and we provide a huge range of specialties across the whole of the Northern region, and in some cases beyond. In terms of our fleet size, we don't have a huge in-house fleet. Mostly estate vehicles, catering vehicles and the like. The fleet itself is quite small - but we do run lease schemes. So we've got about 200 business cars out and about - so that's for community nursing provided across the region. But we also, as a result of that, have quite a significant amount of grey fleet - not so much to go out and visit the community but more for staff moving between the two major hospital sites we have. So in terms of fleet, we've got to be conscious of all that movement.
Then there's obviously the pressures of car parking. We've got 120,000 outpatients coming through the doors. We've got 16,000 staff. And I don't have 16,000 spaces. So we've got to try and accommodate all of those vehicles and all of those movements within approximately 3000 spaces between the two hospital sites. We have a large courier contract for moving all goods and specimens. So there's a lot goods and specimens moving, and in response to Covid-19 we've actually been delivering drugs to patients, to prevent longer queues within the hospital, or a need to travel in just for drugs. We also have a taxi contract, which we manage. And that's used a lot by staff patients as well. And then, in addition to all of that, we have our active travel, making sure that we're providing adequate cycle parking, bike-to-work schemes and the like. So we have to do all of that as well.
Simon: Yeah - it sounds like a huge role David. And I know when we've been talking previously, you told me that maybe a lot of the other trusts split these responsibilities across multiple people and departments. So, is there a benefit to you having it all controlled by one area of the organisation?
David: I think so and I've picked this up in my role as the chair of the NPAG groups that I attend - when transport's fragmented, if you've got different departments running courier and taxi and the likes, you don't have your eye on everything. And it ends up being a huge financial cost to the Trust, because there's replication of services. You've got individual departments or areas using different types of transport - and not always necessarily the right choice. So, to have it all brought under one roof, the benefit is we're very aware of the vast majority of transport movements and requirements for logistics and movement of staff etcetera within our organisation. And that helps us to make sure that we're choosing the right kind of transport, or managing costs. We're trying to keep everything joined together, and that has a huge advantage.
Simon: So with such a large remit then, what do you focus on most?
David: If I'm honest, car parking probably is about 10% of the role, but takes about 90% of my time - because it is so sensitive and contentious within the NHS. So car parking takes a great deal of my time. But most recently as well, we've introduced the new 'Driving at Work' handbook, so we've got to be aware of changes to the law and changes to the way things are going, to make sure the organisation is safe, and that our staff who are using these vehicles are safe, and correctly insured and mobile. So, the bulk of my time tends to be taken up on car parking, but I do focus quite a bit on how we're going to go forward with additional EV infrastructure. And we were the first trust in the world to declare a climate emergency - so there's a real drive at the moment to get our carbon emissions down, there's a lot of focus on the business miles that are being done; the trips that are being done to and from the hospital by staff, patients and visitors; and the use of our own vehicles as well.
Simon: You mentioned you got a new 'Driving for Work' policy - so presumably ensuring everything's done properly and your legal responsibilities are met is pretty important. What are the main challenges you face with the policy and that kind of thing?
David: If I'm honest with you, the main challenge we face with the policy is probably raising awareness. We have an organisation with 16,000 staff, there's a lot of cross-site movement, and it's making sure that where we do have staff who are using their cars for work - and that can be simple things from driving from one site to another, or going to a meeting in their car – understanding that is business use. And we've found ways of integrating them into parking policy, so no one will get a dual-site permit unless we've got confirmation that all of those checks have been done. And at the moment with our appraisal process - policies are being updated, and I'm integrating these changes into the appraisal process as well.
Simon: That's really good that you include it in the appraisal. So presumably driver communication is a key part of the role then. Hospital trusts, traditionally, are really big employers, aren't they? So, give us an idea of scale for the Newcastle Trust, and how big a challenge driver communication is, so that you can ensure standards are met across the whole workforce.
David: Well, the size of the organisation - we are one of the largest trusts in the UK. And we have 16,000 staff - a large number of staff who are using their vehicles for work - so, we have decided that the most appropriate way to make sure that we raise awareness of this policy, and raise awareness of staff responsibilities and organisation responsibilities to ensure the staff are safe, is to build into the annual appraisal process. Every member of staff is asked, as part of their appraisal, 'are you ever using your car for work, and if you are, you need to do X, Y and Z... and you must be aware of this policy', and the manager knows that those licence checks, those insurance checks, those vehicle checks have to be done on a daily basis. And then they're accountable for it as well, to prove that those checks are done.
Simon: So, how big is your grey fleet?
David: Well, I would estimate that my grey fleet's probably in the region of about 4500 - 5000 vehicles.
Simon: Wow.
David: There's a risk that those staff, because they have their cars at work, will use it to go to a meeting, or use it to go and quickly run something somewhere else, or use it to go and run to the hospital.
Simon: Yes. And I wanted to talk a little bit about fatigue, because that's often identified as a common problem for staff with long shifts and night work. How much of a problem is fatigue for your trust? And how do you try to manage that from a road risk perspective?
David: There's obviously other policies within the organisation around health and wellbeing, and supporting staff. There's a European Working Time Directive, which is applied to medical staff, and obviously their hours. And often there are managers, and I can only speak for my own staff as well, where you don't necessarily know what someone's home life is like, and what their quality of sleep is like, and how they're living their life. But you would hope as managers that you are picking up signs of fatigue from staff.
Simon: I've heard of a couple of cases, for instance, where people... surgeons or consultants have actually been involved in fatal accidents on the way home because they're too tired. And I think this is common in any walk of life, not just the NHS. But, the shift pattern probably makes it quite a common challenge in the NHS, where people are working long shifts and they are really tired, and maybe they should stay overnight somewhere or have a rest. But there's that instinct - "I've got to get home, I want to see my family, I want to sleep in my own bed" - but they're too tired really to drive home. And actually, even if they do drive home, the journey might be such that they don't get enough sleep before they're back on for another shift the next day. Do you have policies to try and mitigate that?
David: Yes. As I say, our working time directives and the likes - policies are there, we've got policies around the health and wellbeing of staff, even coming down to our taxi policy... Our taxi policy is also geared then to say "we will provide taxis to staff if there's fatigue... if they've worked long shifts and they're not up for driving". All of those support mechanisms are there. The challenge remains, I suppose, of letting everyone know what is available, and what they should be looking at, and what they should be doing.
Simon: Everyone's working environment has been turned on its head in the last year, obviously because of Covid. How has that impacted on your operations, with the various restrictions to do business as normal?
David: I think the past 14-15 months has been an incredibly challenging time for everyone, and the NHS as well. But the changes operationally, I suppose... we've had less vehicles coming into the organisation. We've had big challenges on car parking, obviously, as public transport was restricted and staff were naturally very nervous about coming into work on public transport and then potentially spreading infection into the hospital. And obviously a lot of the community work slowed right down as well, because there was no face-to-face contact. We're slowly moving back into a period of recovery, and this is actually proving more challenging than the changes we had to make for Covid in the first place.
Covid is still here, but we've got waiting lists and we need to start driving up our activity again, to concentrate on helping patients with other medical conditions that still exist. But what's interesting in the way that we've changed... what we're doing now we're having Zoom calls and podcasts, and it's much more commonplace to have meetings remotely. We have staff working at home as well. There has always been this challenge of "we must have this meeting" and you all go sit around the table and meet. Now people are used to using Teams. So you'll certainly see those changes in business travel coming forwards. We will see reduced business travel, of that I have no doubt.
Simon: What about patient services, then, if people are less likely to come in, because they can't get in maybe, or they don't want to use public transport? How are you supporting patients?
David: So we now have a much higher level of remote consultations as well. We now have patients who are being seen remotely, using various multimedia platforms, or telephone calls and the like. And even our outpatient medicines deliveries - we're delivering up to 3000 prescriptions per month to patients. And a lot of them are hospital-only drugs, so they can't be collected at the local pharmacy. We're avoiding that queuing at pharmacies, and additionally we're actually saving the trip into the hospital - because in some cases, patients were coming into the hospital solely to pick up the hospital drugs so all of those trips can be reduced as well.
Simon: And are you using your own vehicles and drivers for that drugs delivery service?
David: Yeah, we have a Trust courier contract, and we're using them. But we've also started using volunteers. So we now have volunteers also delivering that service for us.
Simon: Wow. So, with that service you've got, presumably, normal courier services with cars and vans, and we've mentioned taxis before so you plainly use quite a lot of external transport providers, and I guess you use some for patient services as well as for the drug delivery service we've just been talking about. And it looks like that's grown quite a bit over recent months. There's something I refer to as procured transport, where you're subcontracting out the delivery of the actual transport service itself, but you're not necessarily outsourcing the risk - you've still got overall responsibilities to ensure that service is delivered. And you've kind of referred to that with making sure your volunteers understand the rules. Do you vet these providers - couriers and taxi firms - to ensure they're managing their own risks properly?
David: Oh, absolutely. It's key. It's a key part of the tender specification. But it's also a key part of their key performance indicators that they give us at their review meetings, where we're asking for evidence that this work is being done and maintained. It's very easy for anyone to tick a box to say "yes, we'll do X, Y and Z", but there's very much a responsibility on us as an organisation to make sure that they're doing exactly what we've asked them to, in terms of driver checks, vehicle tracking, vehicle checks. Our courier company are doing significant miles, and it's vital that we set that objective to our transport providers to make sure that they're fully aware of the risks, and then to evidence them when we meet them.
Simon: Yeah, I think it's really important - and especially when you're, effectively, paying these people with public money, and so it's only right that it's expected that they manage that work-related road risk to a legally compliant and appropriate level, isn't it?
David: Yeah, and very important as well is they still represent our organisation. They are still a representative of Newcastle-Upon-Tyne Hospitals, because by right they are delivering Trust services. And therefore, what we expect of these transport providers and what we expect of the service is very much an awareness that our name is still on the door. They are representatives of this organisation, and we expect the same levels of quality, professional and compassionate care and service delivery for our patients.
Simon: Just looking to the future for a moment, what do you think your biggest challenges are going to be in the years ahead?
David: Well we've already implemented a diesel ban - so none of our new fleet vehicles coming through can be diesel. And at the moment, we're actually quite far down the line to progressing that to a total combustion fuel engine ban.
We've started to try and move away from combustion fuels altogether. I think that's a challenge at the moment on larger vehicles, such as vans, because the market doesn't yet have the EV range needed for everything - particularly vans. But that will certainly change, the market will lead itself on that, and that will change and we'll be able to implement that much more readily in the next couple of years. Even on our salary sacrifice scheme - where staff can lease cars to the organisation, in essence - we're looking for that to be only ULEV or ZEV vehicles; zero-emission or ultra-low emission vehicles only available to lease.
Simon: This links in with something you said earlier, about your targets for reducing your environmental footprint and working towards net carbon zero. You're the first healthcare authority to set these really quite stringent targets, aren't you?
David: We are, yes. We were the first healthcare authority in the world, I believe, to declare a climate emergency. And we have a sustainability manager in this organisation who is incredibly driven to make us succeed, and really lead the way in our drive to reduce our emissions - and to achieve net carbon zero. It's something we're all very passionate about, it's embedded in the organisation - this ethos that everything is very much around that. And our own chief executive, Dame Jackie Daniel, is very much driving forward the need to be carbon zero. Newcastle University, who are across the road from our main site in the city, they've declared a climate emergency, and our local authority have declared a climate emergency. So we've got a real collaboration of effort on making sure that we can drive down those emissions.
Simon: Yeah - I think it's really important, and it's obviously front-of-mind for most fleets now, that transition to EVs and striving towards net zero for everyone.
David: It is, and there are challenges around making sure that ambulances spend the vast majority of their time at a hospital. And making sure that we put the infrastructure in to enable the ambulance service to transition their fleet, by saying "don't worry when you bring patients to this hospital - you can put some miles into your vehicle to carry on and stay on the road for longer". You know, making sure that we have infrastructure in to keep our courier vehicles charged up via rapid charges and the like, so they can keep delivering our services. Looking towards more [????? 20:22]. But even as far as our taxi contract - we put out the taxi contract and we say "we want to see reduced emissions in all taxi fleet over the next few years, to the point where we say by X year, you will not have any engine combustion taxis allowed to come on this site - we will expect EV".
Simon: When we've talked previously, you've talked as well about trying to reduce the number of transport movements on and off the main hospital site. And, one of the things that you would try to do in the future is to maybe have deliveries in and out of a central hub off- site, and then that would reduce the traffic in and out of the hospital site. Can you tell us a little bit about that?
David: It's something that we're starting to work on. And it's an idea that, I think, many Trusts should be looking at now. All Trusts have huge volumes of goods coming into the hospitals on a daily basis. And invariably, the main process is that those drugs are delivered by HGVs, couriers, LGV vehicles and the likes. And it will take a long time for those vehicles to go EV. But then there's the capacity within the hospital itself, to accept those deliveries, which are then held and then moved internally to the various destinations, via a team of porters on the ground. And I feel that there's a lot of scope in having an off-site consolidation centre - for want of a better word - which means that all deliveries are taken to a central warehouse out of city or whatever, and then we do direct delivery to ward from that consolidation centre, using EV vehicles doing smaller shuttles. What it means is that rather than the goods vehicles coming onto site, and a necessary - potentially clinical - space being taken up... hospitals will grow, the population's growing, and hospitals need to expand so do we use valuable hospital space to move things round, or can that space potentially be used for clinical expansion, with off-site storage at a warehouse for goods and then bringing goods in directly to source and then bringing things back out?
Simon: That sounds like really exciting developments for the future. I've got one final question for you, David. You've been managing transport for many years, and you've got a complex role. So what's the most important thing you've learned about the role in that time? Could you give our listeners one last pearl of wisdom?
David: Yeah. I love what I do, I love the challenge of it - and that comes from me as an individual. I think what I've probably learned most is just how much transport impacts on every aspect of hospital operations. And whether that's the patients coming in; the staff getting to work and getting home; all of the logistics that are involved in bringing everything in and out; and moving patients and services around... without transport - and effective transport - it grinds to a halt. Transport is absolutely a key component of healthcare. It has so many impacts on operations, finances, health and wellbeing. Emissions can affect health, so if we generate more emissions we're actually creating poorer health for the long term. So there's a huge impact. I’ve learned just how much transport impacts on everything but quite surprisingly, how it's not really a major consideration within a lot of organisations.
Simon: It's so important. David, I really appreciate you sharing your insights with us - thank you so much for being on the show.
David: Thank you for having me.
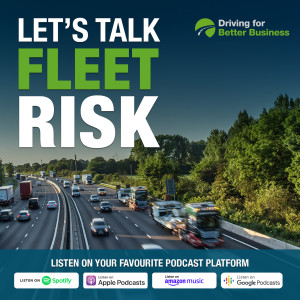
Thursday Sep 09, 2021
Driver Distraction: An inconvenient truth
Thursday Sep 09, 2021
Thursday Sep 09, 2021
Show notes
In this episode of Let’s Talk Fleet Risk, Simon Turner discusses the thorny issue of driver distraction with Dr Gemma Briggs from the Open University.
Gemma is an applied cognitive psychologist who has been researching driver inattention for over 15 years. She has lectured and written extensively on the attentional and perceptual issues caused by phone use when driving and has worked closely with several road safety charities to promote and share research findings.
Gemma and Simon discuss why a driver on the phone will suffer from 'inattention blindness'
What does the science say about our ability to multitask and take a call whilst driving
They look at the shared responsibility between employers and drivers, and their social responsibility to other road users, and discuss how management can often undermine the whole process.
Finally they look at some of the free resources that are available to help employers and drivers to understand and combat distracted driving
https://www.drivingforbetterbusiness.com/podcast/episode/driver-distraction-the-inconvenient-truth/
Useful Links
Driving for Better Business Resources on driver distraction and using mobile phones while driving
Search Results - Driving for Better Business
Driving change website: https://drivingchange.webflow.io/
Can you count the cars challenge: https://youtu.be/XRXdmmTk32I
The mobile office challenge: https://www.open.edu/openlearn/health-sports-psychology/psychology/are-you-driven-distraction
Video on distracted driving: https://www.youtube.com/watch?v=DzYAOOyVp7w&list=PLiUzMkrWK6CuyHzDV2ShdYEQgBYNC1N3B&index=2&t=8s this was linked to a brainteaser task (see attached) where people are asked to rate the behaviours in order of danger when driving.
The Inconvenient Truth About Mobile Phone Distraction: Understanding the Means, Motive and Opportunity for Driver Resistance to Legal and Safety Messages: https://academic.oup.com/bjc/advance-article/doi/10.1093/bjc/azab038/6262317?login=true
Transcript
Simon: Welcome to Let’s Talk Fleet Risk – a podcast for those who manage drivers and their vehicles, and want to reduce road risk in their organisation. I’m Simon Turner, and I’m the campaign manager for Driving for Better Business. In this episode, we’re going to discuss the thorny issue of driver distraction with Dr Gemma Briggs from the Open University. Gemma is an applied cognitive psychologist who has been researching driver inattention for over 15 years. She’s lectured and written extensively on the attentional and perceptual issues caused by phone use when driving, and has worked closely with several road safety charities to promote and share her research findings. Gemma and I are going to discuss why a driver on the phone will suffer from inattention blindness; what the science says about our ability to multitask and take a call while driving; we look at the shared responsibility between employers and drivers, and their social responsibility to other road users; and we also discuss how management can very often undermine the whole process. And finally, we look at some of the free resources that are available to help employers and drivers understand and combat distracted driving.
(transition)
Simon: Hi Gemma, and welcome to the podcast!
Gemma: Hi! Thanks for having me.
Simon: So Gemma, perhaps you could start by just telling us a little bit more about the type of research that you do.
Gemma: Sure. I’m a cognitive psychologist, and predominantly I’m really interested in how people pay attention, and how they perceive dynamic and changing scenes. The biggest application of that theoretical basis for me is looking at mobile phone use by drivers, so I’m really interested in what happens within a driver’s brain while they engage in a secondary task, such as having a conversation on the phone. I’m interested in what they do with their attention – do they try to divide their attention? Now research has looked into whether that’s actually possible or not – or whether – more likely perhaps – they shift their attention between those two tasks, and what that means for their performance in both tasks. How does their driving performance deteriorate? How does their performance in the phone conversation cope? How well do they cope with that situation – and what do they get out of it? What we’ve been able to share, which I’m sure we’ll talk about in more detail later anyway, is that it’s a really big problem in terms of driving performance. When we try to divide or shift our attention in this way, we can come unstuck.
Simon: Yeah. I doubt there’s anyone listening to this who doesn’t know that using a handheld phone while driving is illegal, but using a hands-free phone is legal. The implication of that for many is that hands-free is safe – or it wouldn’t be legal. So is it safer? What does your research show?
Gemma: Sure. So in research terms – it’s certainly not just my research or my collaborative research that’s looked into this – but what we do know is that hands-free phone use offers no safety benefit over handheld phones. So regardless of whether you’re physically holding your phone or not, you’re 4 times more likely to be involved in some kind of incident or crash. Your hazard perception ability vastly decreases. Your eye movements will change – so you’ll look around the scene less, and that can have implications for what you see and you don’t see. And those hazards that you do notice, you’ll take significantly longer to react to. So our research that I’ve done collaboratively largely with Graham Hole from the University of Sussex has looked into some of the specifics of that.
We wanted to identify – we know this is a problem, but why is it a problem? And it seems that it’s cognitive distraction that’s the issue. It’s not really whether you have both hands on the steering wheel and both eyes on the road ahead, because what we’ve been able to identify is that you can be in that situation – hands appropriately on 10 to 2 on the wheel and eyes looking at the road ahead – but if your mind is elsewhere, on a phone conversation, then you can miss things that happen right in front of your eyes. One particular experiment that we carried out put drivers in a driving simulator, and we tracked their eye movements. And we had this theory that perhaps the mobile phone conversation is drawing on cognitive resources that are actually needed for the driving task, and that’s why there’s a problem in terms of noticing and reacting to hazards. So, we asked some of our participants to complete a secondary task – a phone task, hands-free – which induced imagery. We asked them things like “true or false: in a rowing boat, a rower sits with his back to the front of the boat?”, “do cows have hanging ears?”. All of these kind of things that in order to answer, you probably have to conjure up an image in your head. We had another group of participants who weren’t distracted, and yet another group of participants who were distracted by non-imagery inducing statements – things that you either know or you don’t know, and they needed to verify. So, “the capital of Spain is Madrid”. Things that you probably don’t need to picture. And what we found was that it seems when people have a mobile phone conversation, they tend to picture their conversation partner; where they are, what they’re discussing, what they’re talking about, and you spontaneously create these mental images. The same brain areas that are needed for visual perception are also needed to create these mental images, and that can explain why a driver can look directly at something – and we know they’ve looked directly at it because we’ve tracked their eye movements – yet they’ve failed to react to it. When you ask them later, they say they didn’t see it – so in that particular experiment, those participants who were distracted by imagery inducing statements noticed far fewer hazards than any other participants. Those who were distracted by non-imagery were also worse than those who drove undistracted. But those distracted by imagery showed the worst performance overall. So, they either didn’t spot hazards, or if they did, they took up to a second longer to react to them, even if that hazard occurred right in front of them where we could demonstrate that their eye was directly pointed and trying to take in that information. It demonstrates a phenomenon known as inattention blindness; looking without seeing, so from that research – and we’ve built on that, and many others have done relevant work in that area – we can say that drivers on the phone, whether handheld or hands-free, can suffer from inattention blindness. They can look directly at things, yet not see them – and because they don’t see them, they don’t react to them.
Simon: So is that because the brain can’t physically hold two images at once? It can’t process the visual information from what’s going on in front of the driver at the same time as creating this mental image – it’s kind of one or the other?
Gemma: Kind of. I think it’s probably fair to say that the brain can attempt to process both things at once. But I think the issue is that we tend to try and think of our brain as being similar to a computer, in the sense that we can have multiple streams of information being processed at the same time, and that we can divide that beam of attention – but actually, what we know, is that we tend to switch between tasks, rather than divide our attention. That shift can be very quick, so much so that we don’t necessarily notice it ourselves. But there will be points in time when our brain isn’t actively processing the driving scene ahead of us – the information that we’re taking in – because it’s busy processing something else; a mental image, whatever that might be. So, it’s competition for cognitive resources for these two tasks. Both tasks are drawing on this same pool of resources, if you like, and like in any competition, one task tends to win. So, if it’s the phone conversation task that wins, and takes those visual resources away from the driving task, then the driver’s eyes can be on the road, but they’re not processing that information all the time.
Simon: So that sounds like we’re talking about, effectively, multitasking there, doesn’t it?
Gemma: Exactly.
Simon: And many people believe they can multitask – “I can drive and I can use the phone at the same time” – is that not true?
Gemma: It’s not that it’s not true, it’s that I think our understanding of what multitasking is, is distinct and different to what we know about how the brain works. What we know about multitasking is that yes, sometimes we can maintain a couple of tasks at the same time, but what we’re doing is we’re shifting between those two tasks. We’re not keeping them going at a constant level simultaneously. We’re shifting. What we also know is that when we multitask, generally speaking, both tasks will be performed worse than if we tried to do them individually. So it’s far better, cognitively speaking, to focus on one task and then do another, rather than trying to do them simultaneously. Of course, that’s not practical all the time in everyday life. So we talk about multitasking, and we talk about the importance of multitasking, but our understanding of what that means is quite different from what our brain can actually achieve.
Simon: So, if drivers who haven’t had an accident while they’re on the phone – and there are obviously many of those – it’s kind of believing that they’re a bit invincible. They think “I haven’t had an accident so far…”. It sounds like they’re not recognising the fact that they’ve missed so much of what’s been going on while they’ve been on the phone. They don’t perceive there’s a risk, because they haven’t been aware of the risk while it was happening.
Gemma: Absolutely – that taps into a really key thing in this whole piece of research, which is that around 80% of drivers consider themselves to be better than average at driving – which, statistically is possible but is also highly unlikely! Someone needs to be average, someone needs to be below average. So, if you’re driving along and you haven’t had a crash, you haven’t been involved in any kind of incident, you tend to be – if you’re distracted – unaware of how unaware you are.
What will happen is other road users – whether that be other drivers, pedestrians, whatever – will be compensating for your lack of awareness. So, in the absence of any kind of catastrophic crash – which you obviously become aware of – a distracted driver, generally speaking, will be unaware of how many near-misses they’ve had, how many times they’ve driven too close to the vehicle in front, if they’ve veered out of their lane – so it’s kind of like a confirmation bias for these drivers; the majority think they’re better than average, they’ve never had a crash, they’ve never had an incident whilst using their hands-free phone, therefore they’re fine. And what’s interesting is that same group of drivers – the majority – will comment that they fully support laws banning mobile phone use, banning handheld phone use, and many will even go so far as to say “any type of mobile phone use is really a danger and I can understand that, and other people shouldn’t do it – but not me, because I’m better than average, and I’ve never been involved in any kind of incident”.
So it’s a real tension, because you present data such as ours, empirical data that looks at reaction times and eye movements and all of those kind of, if you like, geeky areas of research that can explain why it’s a problem cognitively. But we’re all human. So when we communicate that to people, it’s quite common, in fact it’s extremely common that there’s a defence of that. You know, this is really inconvenient research. People don’t want to be told that they can’t multitask, because that’s what we’re told we should constantly be doing. And they don’t want to be told that hands-free mobile phone use is any different to talking to a passenger in the vehicle, because this stuff is all pre-installed in their vehicles, and they’re expected to use it by family, friends, employers or whatever. So there’s a real tension between what we understand about how our brain works, and how we can communicate these messages in a convincing way, so that people can’t just say “no, sorry – it’s no different”.
Simon: You mentioned passengers there – one of the most frequent excuses or challenges to this is “well how is phone distraction different to talking to a passenger in the car?”. How is it different?
Gemma: Well it taps into what we said about imagery but also it’s an issue of shared environment. So, a passenger within your vehicle can obviously see what you can see, they can see the challenges that you are facing and can regulate their conversation accordingly. By that, I mean hopefully they will stop talking if they can see that you’re facing a particularly challenging driving situation. Or they might even help – pointing out a vehicle that you haven’t perhaps spotted – whereas someone on the phone doesn’t have the benefit of that shared environment, so they’re going to continue to demand your precious attention. In fact, if you stop talking – which is a common thing; your brain will say I need to process this information, I’m going to stop responding to another task – if you stop talking momentarily on a mobile phone conversation, your conversation partner is likely to say “are you still there?” and demand your attention back to them, so, this issue of shared environment is a big difference in terms of the distraction imposed by a passenger compared to a mobile phone conversation.
Simon: Yeah. I want to delve a little bit now into what employers can do about this. This is one of the major driving at work risks for employers – and I don’t think there are many employers that don’t see it as a risk – they just don’t know how to manage it effectively. And, I had Mark Cartwright on the show recently from Highways England talking about Operation Tramline, which is where the police roam the motorways in unmarked lorry cabs taking film of poor driving behaviour. And one of the most common offences that they see – whether it’s truck drivers, van drivers or car drivers, because it catches offences in all of those different vehicle types – is phone distraction. And a lot of handheld phone use – so employers clearly need to set down rules, and that means putting guidance on mobile phone use in their ‘Driving for Work’ policy. What do you think that guidance needs to include?
Gemma: It’s a really tricky one, because obviously, if you’re driving for work, for a living, then your employer has a responsibility to keep you safe – but of course, it’s kind of a shared responsibility as well. The first thing I always say to people making policy for workplace driving safety is that you need to be aware of that shared responsibility. Your employer needs to be very clear on their position on phone use – and of course, handheld phone use is illegal, so that position should be clear, but it can still be even more clearly communicated – if you are found to be texting at traffic lights, or checking your next drop, or doing any kind of handheld activity on a phone, you will lose your job.
From the flip side, of course, from the employee’s side, it’s your driver’s licence. It’s your job, so there’s that shared responsibility. But in terms of what the policy needs to set out; whether there’s a ban on any type of phone use – which many companies are now taking on board – or if it’s just a ban on illegal phone use – you would hope that the existence of the law would cover that, but as I’ve said, it doesn’t. As you’ve said, it demonstrably doesn’t.
I think there’s a lot to be done in terms of policy relating to education, so explaining why it’s an issue, not just that it is, or that you’ll get sacked if you’re caught using it. There needs to be a level of accountability, but that needs to be explained and made clear to drivers -evidence-based education such as ours can help with that, but in other clear policy terms, we need an agreement between managers and drivers about what is acceptable and what isn’t acceptable. If you have an all-out ban on any type of phone use by your drivers, then you as a manager should not have an expectation that your driver will answer a phone call at any time that you call them. You have to have a clear policy that says ‘at this time in your working day, you need to be parked up and available’. There are big challenges there when we talk about delivery drivers, for example. They have multiple drops, and they need to get updated routes and information like that, so, I’m not naive to the fact that it’s actually a massive challenge if we try to ban any type of phone use in this area – but individual companies must have a really specific, clear policy on what is and isn’t acceptable, that is followed by all members of that organisation. It will sound really obvious, but we know from the Driving for Better Business survey that came out a couple of years ago is that there is a real disconnect between what management expect and what employees expect, and how that ties in with company policy.
Simon: Yeah. I’ve spoken to a number of fleet operators now who have introduced zero tolerance phone policies, and the most common argument for not doing it is that “our staff need to be contactable, we need to be able to update them”. But most of the companies I know that have instigated a zero tolerance phone policy have been able to make it work. They have times when the drivers can stop and get updates. The drivers understand when a safe time to answer the phone and when to update is. And it doesn’t impact their productivity if managed correctly. But I think the key thing in this that you’ve mentioned there, and the survey that we did, showed that 49% of senior executives expected their drivers to answer the phone while driving – and many of those had policies which told the drivers that they weren’t allowed to answer the phone.
So it’s so important that everybody in the company leads by example – if you’ve got the executives disrespecting the policy and phoning up the drivers, then the drivers have no respect for the policy either, do they?
Gemma: Absolutely. A company policy has to apply to every employee, and if there’s even a whiff of the fact that senior executives are allowed loopholes, then you won’t get compliance from other employees because it’s a demonstration that the policy isn’t effective and won’t be enforced. So that comes back to another thing that we know from psychological research – you need a clear policy of course, but if that policy is broken by any employee, you need an appropriate approach to dealing with that. Because otherwise the policy doesn’t work as a deterrent to doing what you shouldn’t be doing. As long as there’s a clear policy, and it’s backed up by deterrents in the sense that “if you’re caught doing this, there will be a consequence, regardless of who you are – the CEO or one of the delivery drivers – there will be consequences”. But in order for that to happen, there needs to be a credible threat of being caught. If drivers know that there’s no way of it being detected that they’re sending a quick text, or they’re answering a phone call from their manager and their manager said “it’s okay, I won’t tell anyone”, then it’s not going to work either. It’s a real challenge. You need that kind of threat – which sounds strong – but you need a threat in order for deterrents to work, and that needs to be backed up by education. So as you’re saying, those companies where they have got an all-out ban, and it is working, and drivers understand why it’s in place and understand when they can stop and take calls, I would assume that that’s because they’ve got a clear policy, and they’ve explained why. People want to know why.
Simon: The resources for drivers – educating drivers is a really good point. We’ve just produced something called the Van Driver Toolkit, which is a series of safety updates for drivers which are free to access for employers – and one of those safety updates is around mobile phone distraction. And it shows the consequences of doing it, there are some helpful tips on how to not do it, it explains – in very simple terms, in a very short piece of collateral – what the drivers need to know so they can make their own decisions, informed decisions, around that. Employers are free to download those and share them with their drivers, so I’ll share the link to that in the show notes at the end.
So, we talked about the survey Driving for Better Business had done earlier, and something else that came out of that survey was that – and I was quite staggered by this statistic – 1 in 6, so 17% of those who drove for work – having surveyed over 1000 drivers; it was a professionally conducted survey – 1 in 6 of them said they’d been involved in an incident while on the phone to their boss or a colleague – so we’ve got the proof that this is quite clearly a problem for businesses. Now, many of those wouldn’t have been injury collisions. But it just shows how reducing phone use can reduce the chance of even damage only incidents, which then disrupt the business and result in expensive damage repairs. I mean, that’s another reason for businesses to look seriously at curtailing phone use while driving, isn’t it?
Gemma: Absolutely. In terms of costs, of course. As you say, not all incidents will involve contact collisions, or they might and you’ve got damage of course. But there’s also the level of social responsibility for companies. Of course the company wants to save money. Of course the company wants to keep their employees safe. But equally, they’ve got a social responsibility to keep other road users safe from their potentially distracted drivers, so there’s a reputational issue as well, of course. You know, all of us who use the roads have this social responsibility to interact appropriately on the road network. Now, again, that might sound very naïve, but that’s how the system ultimately has to work, and when it breaks down it can have quite catastrophic impacts of course. So yes, it’s certainly in the interests of individual companies, as well as wider society, to tackle this problem, because we do know it’s a growing problem; not just amongst people who drive for work, but amongst the general public. Self-reported phone use – handheld and hands-free – is on the up. It’s increasing, and so are the number of police-recorded incidents that are attributed to distraction – so it’s a real problem.
Simon: Yeah, it is. And we’ve seen that from our research as well, and as I say, the Operation Tramline footage that we’ve seen. Gemma, have you got any resources that we can share with listeners that might help them manage phone distraction among their drivers?
Gemma: Yes, certainly – because I’m based at the Open University, we’ve got an online learning platform that’s entirely free, called OpenLearn and myself and my colleague Dr Jim Turner have created a couple of interactive activities that are freely available that sit on OpenLearn. These are evidence-based activities. They’re gamified, if you like. The idea is, it takes about 10 minutes to complete. You go along and you experience distraction for yourself. In the first one that we’ve got, called ‘Are You a Focused Driver?’, you watch a very quick series of clips – some of which may contain a hazard – and you’re asked to look out for those hazards. And at the same time, you receive a phone call from a very demanding friend who’s giving you a shopping list of things that you need to remember. The idea is that you’re engaging in a cognitively demanding task, as well as driving – as well as looking for hazards. You’re then asked a couple of questions about that phone task, about what you remember, because we want to know how you perform on both tasks. And then you’re asked about which hazards you notice and which you don’t, and people are given immediate feedback, so they get a score for their phone conversation answers and they get a score for their hazard perception. It’s been done by thousands of people. What we’ve found is that people tend to do well in one task or the other, not both. Which is entirely backing up the research that we’ve done, and many others have done too, so it’s a nice little fun and non-judgmental approach to education, and once you’ve completed the task, there are further links where you can find out more information. There’s a video of me talking about research in this area, and again, explaining why it’s a problem and why you might have just completed this and not done too well.
The second one we launched at the end of last year. It was called ‘The Mobile Office Challenge’ and this one might be particularly relevant to people who drive for work of course. The idea is that, obviously a lot of people drive for work, so their car does in effect become a mobile office. And in this one we were quite interested in looking at driver confidence that you’ve noticed all of the hazards, and that you’ve performed well in that phone conversation. Without giving too much away – you are put in the position, you’re told that you’re a wedding planner driving between appointments and you receive a phone call from a couple whose wedding you’re planning, so that you can plan their wedding appropriately. At the same time, you need to look out for hazards, and then you’re asked some questions along the way; how confident are you that you’ve noticed all of these hazards? How confident are you that you can meet your client’s needs. Again, unsurprisingly, we found that people tend to do well in one or the other task. In this one, there’s a nice distinction because you get to first complete this hazard perception task with a phone conversation, and then you do it without a phone conversation, so you can compare your own performance between being distracted and not being distracted. In terms of hazard perception and how well you do, unsurprisingly, those doing just the hazard perception task tend to perform much better. And then again there’s more information and more links and FAQs at the end. The idea is that these are freely available, they’ve been adopted by various police forces who have used them as roadside education tools, for example. The idea is that it’s explaining why it’s a problem – not just that it is – and allowing people to witness their own distraction, which means they can’t then say “yeah, but this doesn’t mean me”.because they have seen their results themselves.
Simon: Those sound fantastic. I’ve seen some of those myself and we’ve got them on the Driving for Better Business website, so I’ll make sure all of the links to those resources are in the show notes, so listeners can access those and download them. Gemma, phone distraction is obviously one of the key things that employers and fleet operators have got to manage – I really appreciate you sharing your insights with us. That has been fantastic, thank you so much for being on the show.
Gemma: You’re welcome, thanks for having me.
Simon: And thank you everyone for listening!